Punching head and manufacturing method thereof and composite small grinding head
A manufacturing method and punching head technology, which are applied to grinding devices, manufacturing tools, grinding machine parts, etc., can solve the problems of difficult to guarantee precision, low brazing strength, poor practicability, etc. The effect of improving connection strength and service life
- Summary
- Abstract
- Description
- Claims
- Application Information
AI Technical Summary
Problems solved by technology
Method used
Image
Examples
Embodiment 1
[0057] like Figure 1 to Figure 7 As shown, a method for making a punching head includes the following steps:
[0058] Step 1. Arrange the two first outer molds 4 in parallel, and put the sintered body powder mixture 3 between the two first outer molds 4; arrange the two second outer molds 6 between the two first outer molds 4 , the two second outer molds 6 are respectively located at both ends of the sintered powder mixture 3; the mold frame 7 is then fitted around the two first outer molds 4;
[0059] Step 2. Two sheet-shaped indenters 5 are located between the two first outer molds 4, and are respectively located at the upper and lower ends of the sintered body powder mixture 3; The mixture 3 is compressed, and the sintered body powder mixture 3 is laterally compressed, and the sintered body powder mixture 3 is compressed into a powder metallurgy sintered body 8 with a cuboid structure;
[0060] Step 3. The upper end of the cuboid-structured powder metallurgy sintered bod...
Embodiment 2
[0071] like figure 1 , figure 2 , image 3 , Figure 8 , Figure 9 and Figure 10 As shown, a method for making a punching head includes the following steps:
[0072] Step 1. Arrange the two first outer molds 4 in parallel, and put the sintered body powder mixture 3 between the two first outer molds 4; arrange the two second outer molds 6 between the two first outer molds 4 , the two second outer molds 6 are respectively located at both ends of the sintered powder mixture 3; the mold frame 7 is then fitted around the two first outer molds 4;
[0073] Step 2. Two sheet-shaped indenters 5 are located between the two first outer molds 4, and are respectively located at the upper and lower ends of the sintered body powder mixture 3; The mixture 3 is compressed, and the sintered body powder mixture 3 is laterally compressed, and the sintered body powder mixture 3 is compressed into a powder metallurgy sintered body 8 with a cuboid structure;
[0074] Step 3. The upper end o...
Embodiment 3
[0085] A punching head, the punching head 2 is made of impregnated multi-layer diamond.
[0086] The punching head made of the sintered body is an impregnated multi-layer diamond with a self-sharpening grinding layer; the service life is greatly improved, so that the other grinding sections of the composite small grinding head can be fully utilized.
PUM
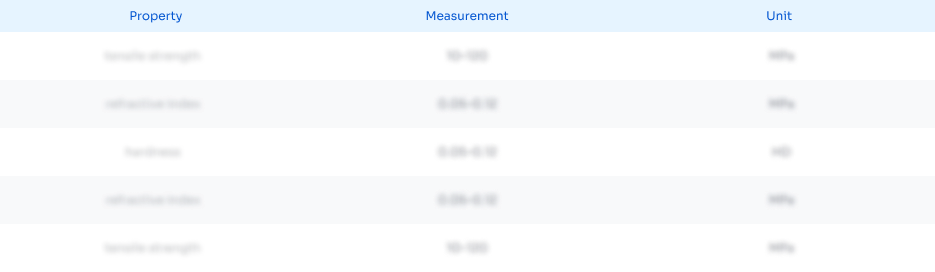
Abstract
Description
Claims
Application Information

- R&D
- Intellectual Property
- Life Sciences
- Materials
- Tech Scout
- Unparalleled Data Quality
- Higher Quality Content
- 60% Fewer Hallucinations
Browse by: Latest US Patents, China's latest patents, Technical Efficacy Thesaurus, Application Domain, Technology Topic, Popular Technical Reports.
© 2025 PatSnap. All rights reserved.Legal|Privacy policy|Modern Slavery Act Transparency Statement|Sitemap|About US| Contact US: help@patsnap.com