Protective grease for bridge inhaul cables, and preparation method thereof
A technology for bridge cables and protective grease, which is applied in the petroleum industry, lubricating compositions, etc., can solve problems such as aggravated grease separation, poor high temperature resistance, and negative impact on engineering, and achieves strong salt spray resistance, good antirust effect, good stability effect
- Summary
- Abstract
- Description
- Claims
- Application Information
AI Technical Summary
Problems solved by technology
Method used
Image
Examples
Embodiment 1
[0071] A protective grease I for bridge cables and its preparation method:
[0072] The protective grease I for bridge cables is a mixture composed of the following components. In the mixture, the content ratio of each component material is calculated as follows in parts by weight:
[0073] 15 parts by weight of polyamide resin, 25 parts by weight of methylphenyl silicone resin;
[0074] Microcrystalline wax—15 parts by weight of No. 90 microcrystalline wax, 5 parts by weight of polytetrafluoroethylene micropowder;
[0075] 8 parts by weight of naphthenic mineral oil;
[0076] High temperature resistant alkaline filler—12 parts by weight, including 6 parts by weight of talcum powder and 6 parts by weight of dolomite;
[0077] Tackifier-18 parts by weight of ethylene-propylene copolymer; Antirust agent-6 parts by weight of barium dinonyl naphthalene sulfonate;
[0078] Antioxidant—2,6-tertiary butyl-4-methylphenol 2 parts by weight,
[0079] Flame retardant—17 parts by weig...
Embodiment 2
[0088] A protective grease II for bridge cables.
[0089] The protective grease II for bridge cables is a mixture of the following components. In the mixture, the proportion of each component material is calculated as follows in parts by weight:
[0090] 18 parts by weight of polyamide resin, 30 parts by weight of methylphenyl silicone resin;
[0091] Microcrystalline wax—10 parts by weight of No. 95 microcrystalline wax, 4 parts by weight of polytetrafluoroethylene micropowder;
[0092] 10 parts by weight of naphthenic mineral oil, high temperature resistant alkaline filler -- 15 parts by weight of calcium carbonate;
[0093] Tackifier—23 parts by weight, including 20 parts by weight of polymethacrylate, 3 parts by weight of petroleum resin;
[0094] Rust inhibitor——10 parts by weight, including 7 parts by weight of barium petroleum sulfonate, 3 parts by weight of magnesium lanolin soap;
[0095] Antioxidant——4,4'-bis(α,α'-dimethylbenzyl)diphenylamine 3 parts by weight;
...
Embodiment 3 Embodiment 8
[0105] A protective grease for bridge cables:
[0106] The protective grease used for bridge cables is a mixture of the following components. In the mixture, the proportion of each component material is calculated as follows in parts by weight:
[0107] 19-28 parts by weight of polyamide resin, 12-29 parts by weight of methylphenyl silicone resin,
[0108] 8-20 parts by weight of microcrystalline wax, 3-15 parts by weight of polytetrafluoroethylene micropowder,
[0109] 5-15 parts by weight of naphthenic mineral oil, 8-20 parts by weight of high-temperature-resistant alkaline filler,
[0110] 10-25 parts by weight of tackifier, 5-15 parts by weight of rust inhibitor,
[0111] 3-5 parts by weight of antioxidant, and 5-20 parts by weight of flame retardant.
[0112] In each embodiment, for the specific content of each component, please refer to the attached table 1 "List of the content of each component (calculated in parts by weight) of the protective grease used for bridge ...
PUM
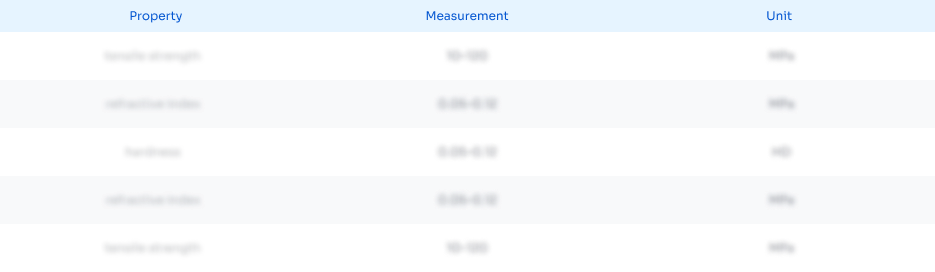
Abstract
Description
Claims
Application Information

- R&D
- Intellectual Property
- Life Sciences
- Materials
- Tech Scout
- Unparalleled Data Quality
- Higher Quality Content
- 60% Fewer Hallucinations
Browse by: Latest US Patents, China's latest patents, Technical Efficacy Thesaurus, Application Domain, Technology Topic, Popular Technical Reports.
© 2025 PatSnap. All rights reserved.Legal|Privacy policy|Modern Slavery Act Transparency Statement|Sitemap|About US| Contact US: help@patsnap.com