Preparation method of high-strength flame-retardant waterproof glass wool
A glass wool and high-strength technology, applied in glass manufacturing equipment, manufacturing tools, etc., can solve the problems of poor flame retardancy of glass wool, high brittleness of glass wool, general waterproof performance, etc., to enhance toughness and mechanical strength, reduce Brittleness, effect of improving impact resistance
- Summary
- Abstract
- Description
- Claims
- Application Information
AI Technical Summary
Problems solved by technology
Method used
Examples
Embodiment 1
[0034] Preparation of mixed slurry:
[0035] Bagasse and wheat straw were put into an oven at a mass ratio of 5:1, dried for 3 hours at a temperature of 60°C, and then put into a pulverizer after drying to obtain a mixed material. The mixed material and hydrochloric acid with a mass fraction of 6% were pressed Put it into a beaker with a mass ratio of 1:10, stir with a stirrer at a speed of 400r / min for 60min, place the beaker in a microwave oven after stirring, and microwave for 10min at a power of 600W to prepare a mixed slurry;
[0036] Preparation of oxidation reaction solution:
[0037] Place the above beaker in an ice-water bath, add dropwise sodium hydroxide solution with a mass fraction of 10% to the beaker to adjust the pH value to 11, raise the temperature of the water bath to 80°C, and react at a constant temperature for 40 minutes to prepare a reaction mixture. Add the sodium hypochlorite powder of reaction mixture liquid quality 2% in the beaker, stir 30min with ...
Embodiment 2
[0046] Preparation of mixed slurry:
[0047] Put bagasse and wheat straw into an oven at a mass ratio of 5:1, dry for 3.5 hours at a temperature of 65°C, and put them into a pulverizer after drying to obtain a mixed material. Mix the mixed material with 8% hydrochloric acid Put it into a beaker at a mass ratio of 1:10, stir with a stirrer at a speed of 450r / min for 70min, place the beaker in a microwave oven after stirring, and microwave for 11min at a power of 700W to prepare a mixed slurry;
[0048] Preparation of oxidation reaction solution:
[0049] Place the above beaker in an ice-water bath, add dropwise sodium hydroxide solution with a mass fraction of 12.5% to the beaker to adjust the pH value to 12, raise the temperature of the water bath to 90°C, and react at a constant temperature for 45 minutes to prepare a reaction mixture. Add the sodium hypochlorite powder of reaction mixture quality 3% in the beaker, stir 35min with the rotating speed of 550r / min with agitat...
Embodiment 3
[0058] Preparation of mixed slurry:
[0059] Put bagasse and wheat straw into an oven at a mass ratio of 5:1, dry for 4 hours at a temperature of 70°C, and put them into a pulverizer after drying to obtain a mixed material. Mix the mixed material with 10% hydrochloric acid by mass Put it into a beaker with a ratio of 1:10, stir with a stirrer at a speed of 500r / min for 80min, place the beaker in a microwave oven after stirring, and microwave for 12min under the condition of a power of 800W to prepare a mixed slurry;
[0060] Preparation of oxidation reaction solution:
[0061] Place the above-mentioned beaker in an ice-water bath, add dropwise sodium hydroxide solution with a mass fraction of 15% to the beaker to adjust the pH value to 13, raise the temperature of the water bath to 100°C, and react at a constant temperature for 50 minutes to prepare a reaction mixture. Add the sodium hypochlorite powder of reaction mixture quality 4% in the beaker, stir 40min with the rotatin...
PUM
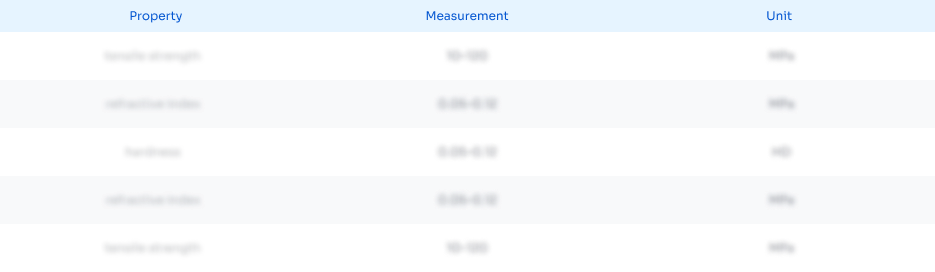
Abstract
Description
Claims
Application Information

- R&D
- Intellectual Property
- Life Sciences
- Materials
- Tech Scout
- Unparalleled Data Quality
- Higher Quality Content
- 60% Fewer Hallucinations
Browse by: Latest US Patents, China's latest patents, Technical Efficacy Thesaurus, Application Domain, Technology Topic, Popular Technical Reports.
© 2025 PatSnap. All rights reserved.Legal|Privacy policy|Modern Slavery Act Transparency Statement|Sitemap|About US| Contact US: help@patsnap.com