Polyvinylidene fluoride coating and preparation method thereof
A technology of polyvinylidene fluoride and coating, applied in the direction of coating, etc., can solve problems such as interface desorption, insufficient wettability of fillers, coating damage, etc., achieve good durability and heat insulation effect, ensure application stability, The effect of good cohesive strength
- Summary
- Abstract
- Description
- Claims
- Application Information
AI Technical Summary
Problems solved by technology
Method used
Examples
Embodiment 1
[0022] Pre-treat the filler before configuring the polyvinylidene fluoride coating: take 3g hollow glass beads, 5g hollow ceramic beads, and 3g aluminum silicate fibers; select zinc acetate as the surface treatment catalyst, and the amount is 0.08g; select 3-methacryloyl Oxypropyltrimethoxysilane is the surface treatment agent, and the amount is 0.8g; ethanol is selected as the solvent, and the amount is 110g.
[0023] Treatment of packing: add hollow glass beads, hollow ceramic beads, aluminum silicate fiber, ethanol, and zinc acetate into the reaction vessel, heat to 55°C, add 3-methacryloxypropyltrimethoxysilane dropwise, Adding time is 40 minutes; after dripping, keep at 55°C for 2 hours, discharge the material and filter, and evaporate and dry the filtered filler under forced convection conditions.
[0024] Then take 16 g of polyvinylidene fluoride resin (melting point 165°C) and 6.9 g of polyacrylate resin with a molecular weight of 2500; the selected solvent is: a mixed solu...
Embodiment 2
[0026] Pre-treat the filler before configuring the polyvinylidene fluoride coating: take 12g of hollow glass beads and 1g of mica powder; select sodium ethoxide as the surface treatment catalyst, with an amount of 0.02g; select 3-methacryloxypropyl triethoxy Silane is the surface treatment agent, the dosage is 0.5g; ethyl acetate is selected as the solvent, the dosage is 100g;
[0027] Add hollow glass beads, mica powder, sodium ethoxide, and ethyl acetate into the reaction vessel, heat to 55°C, and add 3-methacryloxypropyltriethoxysilane dropwise for 30 minutes; After the completion of heat preservation at 40°C for 3 hours, the material is discharged and filtered, and the filtered filler is evaporated and dried under forced convection conditions.
[0028] Then take 17g of polyvinylidene fluoride resin (melting point of 165℃) and 7.5g of polyacrylate resin with molecular weight of 4000; select solvents: 10g of methyl isobutyl ketone, 33g of N methylpyrrolidone, and 20g of dimethylf...
PUM
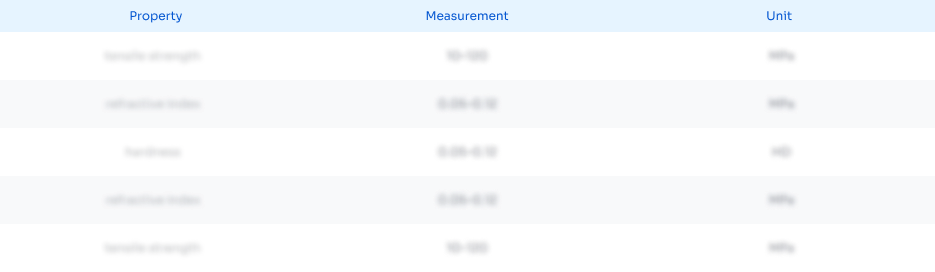
Abstract
Description
Claims
Application Information

- R&D Engineer
- R&D Manager
- IP Professional
- Industry Leading Data Capabilities
- Powerful AI technology
- Patent DNA Extraction
Browse by: Latest US Patents, China's latest patents, Technical Efficacy Thesaurus, Application Domain, Technology Topic, Popular Technical Reports.
© 2024 PatSnap. All rights reserved.Legal|Privacy policy|Modern Slavery Act Transparency Statement|Sitemap|About US| Contact US: help@patsnap.com