Selective laser melting forming method of multi-material part
A laser selective melting, multi-material technology, applied in the field of parts forming process, can solve the problems of low bonding strength between materials, too simple shape of parts, and few types of materials to choose from, to increase the optional range and increase the bonding strength. , the effect of high-precision forming
- Summary
- Abstract
- Description
- Claims
- Application Information
AI Technical Summary
Problems solved by technology
Method used
Image
Examples
Embodiment 1
[0045] Forming of a copper and stainless steel sandwich part:
[0046] S1: Part model design:
[0047] When modeling, in the modeling software, according to the functional properties of the parts to be designed, the copper and stainless steel materials are combined and arranged, and the design criteria of strength, weight, size and other related factors are integrated to optimize the overall design. A part model with information such as material distribution, structural features, datum positions, and dimensional data.
[0048] S2: Acquisition of process model: According to the shape, size and stress change rules of copper and stainless steel materials and interlayer characteristics during the laser selective melting and forming process, perform size and shape compensation and chamfering settings on the part model designed in step S1; Add margins to the parts that need to be machined after forming; finally add positioning and anti-deformation supports as needed to obtain a pro...
Embodiment 2
[0056] Forming of a Ti3Al and TC11 gradient part:
[0057] S1: Part model design:
[0058] When modeling, Ti3Al and TC11 materials are combined and arranged in the modeling software according to the functional properties of the parts to be designed, and the design criteria of strength, weight, size and other related factors are comprehensively optimized to obtain the A part model with information such as material distribution, structural features, datum positions, and dimensional data.
[0059] S2: process model acquisition:
[0060] According to the shape, size and stress change rules of Ti3Al and TC11 materials during the laser selective melting and forming process, the size, shape compensation and chamfering of the part model designed in step S1 are performed; after forming, the parts that need to be machined are made Add a good margin; finally, add positioning and anti-deformation supports as needed to obtain a process model including part model information and the above...
PUM
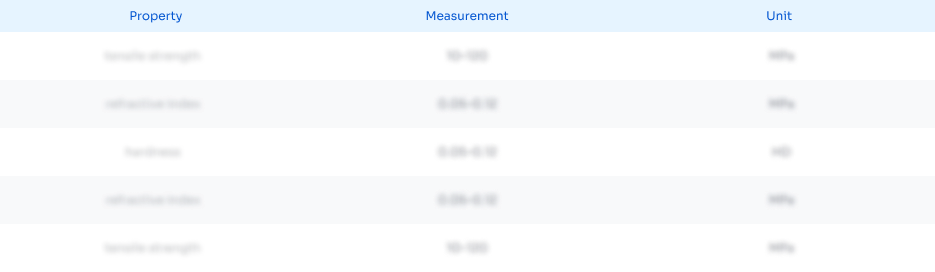
Abstract
Description
Claims
Application Information

- R&D
- Intellectual Property
- Life Sciences
- Materials
- Tech Scout
- Unparalleled Data Quality
- Higher Quality Content
- 60% Fewer Hallucinations
Browse by: Latest US Patents, China's latest patents, Technical Efficacy Thesaurus, Application Domain, Technology Topic, Popular Technical Reports.
© 2025 PatSnap. All rights reserved.Legal|Privacy policy|Modern Slavery Act Transparency Statement|Sitemap|About US| Contact US: help@patsnap.com