A method for preparing wear-resistant coating on steel plate
A wear-resistant coating, steel plate technology, applied in the direction of coating, metal material coating process, melt spraying, etc., can solve the problem of easy peeling of coating and substrate, and achieve the effect of enhanced durability
- Summary
- Abstract
- Description
- Claims
- Application Information
AI Technical Summary
Problems solved by technology
Method used
Image
Examples
Embodiment 1
[0021] This embodiment provides a method for preparing a wear-resistant coating on a steel plate, comprising the following steps:
[0022] Step A: corrode and derust the surface of the steel plate, roughen it by sand blasting, and design a reaction combustion chamber;
[0023] Step B: spraying nickel-chromium alloy on the surface of the roughened steel plate;
[0024] Step C: pressing iron oxide powder and aluminum powder with a mass ratio of 2.9:1 into blocks, and placing them on the above-mentioned sprayed steel plate, and then putting them into the combustion chamber together;
[0025] Step D: preheating the steel plate to 200°C, and then igniting to initiate a self-propagating reaction;
[0026] A ceramic composite steel plate with good bonding strength and wear resistance requirements can be prepared by the above method.
Embodiment 2
[0028] This embodiment provides a method for preparing a wear-resistant coating on a steel plate, comprising the following steps:
[0029] Step A: corrode and derust the surface of the steel plate, roughen it by sand blasting, and design a reaction combustion chamber;
[0030] Step B: Spraying and spraying aluminum bronze on the surface of the roughened steel plate;
[0031] Step C: pressing iron oxide powder and aluminum powder with a mass ratio of 2.9:1 into blocks, and placing them on the above-mentioned sprayed steel plate, and then putting them into the combustion chamber together;
[0032] Step D: preheating the steel plate to 300°C, and then igniting to initiate a self-propagating reaction;
[0033] A ceramic composite steel plate with good bonding strength and wear resistance requirements can be prepared by the above method.
Embodiment 3
[0035] This embodiment provides a method for preparing a wear-resistant coating on a steel plate, comprising the following steps:
[0036] Step A: corrode and derust the surface of the steel plate, roughen it by sand blasting, and design a reaction combustion chamber;
[0037] Step B: Spraying FeNiCrBSi on the surface of the roughened steel plate;
[0038] Step C: pressing iron oxide powder and aluminum powder with a mass ratio of 2.9:1 into blocks, and putting them into a combustion chamber;
[0039] Step D: Preheat the steel plate to 400°C, and then ignite to initiate a self-propagating high-temperature synthesis reaction; through the above method, a ceramic composite steel plate with good bonding strength and wear resistance requirements can be prepared.
PUM
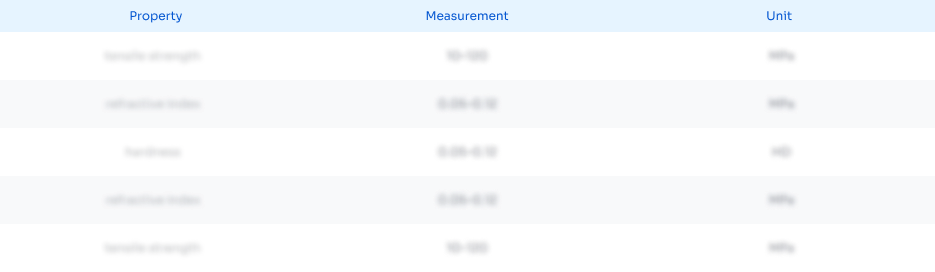
Abstract
Description
Claims
Application Information

- R&D
- Intellectual Property
- Life Sciences
- Materials
- Tech Scout
- Unparalleled Data Quality
- Higher Quality Content
- 60% Fewer Hallucinations
Browse by: Latest US Patents, China's latest patents, Technical Efficacy Thesaurus, Application Domain, Technology Topic, Popular Technical Reports.
© 2025 PatSnap. All rights reserved.Legal|Privacy policy|Modern Slavery Act Transparency Statement|Sitemap|About US| Contact US: help@patsnap.com