Permanent magnet synchronous motor prediction current control method and device
A permanent magnet synchronous motor and current prediction technology, which is applied in motor control, motor generator control, electromechanical transmission control, etc., can solve the problems of complex calculation of non-zero vector action time, error of solution method, error of control method, etc.
- Summary
- Abstract
- Description
- Claims
- Application Information
AI Technical Summary
Problems solved by technology
Method used
Image
Examples
Embodiment Construction
[0077] The specific implementation manners of the present invention will be further described in detail below in conjunction with the accompanying drawings and embodiments. The following examples are used to illustrate the present invention, but are not intended to limit the scope of the present invention.
[0078] figure 1It is a system structure diagram of the present invention, mainly including a DC power supply, a three-phase two-level voltage source inverter, a controller, and a permanent magnet synchronous motor. Among them, the permanent magnet synchronous motor is used as the controlled unit, and the three-phase voltage source inverter is used as the power module to drive the controlled unit. The controller collects the mechanical and electrical quantities of the motor system from the controlled unit, and then uses the control of the present invention The method is used to select the optimal control vector and input it to the inverter through the modulation unit to r...
PUM
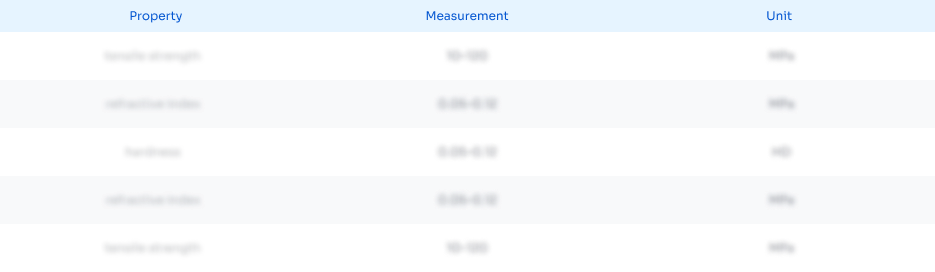
Abstract
Description
Claims
Application Information

- Generate Ideas
- Intellectual Property
- Life Sciences
- Materials
- Tech Scout
- Unparalleled Data Quality
- Higher Quality Content
- 60% Fewer Hallucinations
Browse by: Latest US Patents, China's latest patents, Technical Efficacy Thesaurus, Application Domain, Technology Topic, Popular Technical Reports.
© 2025 PatSnap. All rights reserved.Legal|Privacy policy|Modern Slavery Act Transparency Statement|Sitemap|About US| Contact US: help@patsnap.com