A semi-continuous anti-gravity pouring method for an aluminum alloy automobile frame
An anti-gravity casting and aluminum alloy technology, which is applied in the field of metal processing, can solve the problems of low production efficiency, inability to meet mass production, and low performance of castings
- Summary
- Abstract
- Description
- Claims
- Application Information
AI Technical Summary
Problems solved by technology
Method used
Image
Examples
specific Embodiment approach 1
[0023] Specific implementation mode one: combine Figure 1 to Figure 3 To illustrate this embodiment, a semi-continuous anti-gravity pouring method for an aluminum alloy automobile frame described in this embodiment includes the following steps:
[0024] Step 1: aluminum alloy smelting treatment: perform aluminum alloy smelting, refining, and degassing treatment at the smelting station, and inject the treated aluminum alloy into the crucible 27 in the lower tank 1 for use;
[0025] Step 2: Pre-treatment of the mold: spray paint on the upper half mold 10, the upper mold cavity 11, the core 14, the lower mold cavity 15 and the lower half mold 16, and prepare the riser pipe 23 at the same time, and produce The on-site commander sends an order to the operator of the control center to start pouring;
[0026] Step 3: Horizontal movement of the lower tank: After receiving the pouring order, the operator in the control center manually presses the start button, the trolley 3 carrying ...
specific Embodiment approach 2
[0040] Specific implementation mode two: combination Figure 1 to Figure 3 Describe this embodiment, in the step seven of this embodiment, the lower tank carrying buffer spring 28 is provided between the lower tank running wheel 2 and the lower tank 1, and the lower tank bearing buffer spring 28 is embedded in the lower tank 1 to realize the upper tank. Protection of the running wheel 2 of the lower tank during the descent of the mold movable plate 7. The undisclosed technical features in this embodiment are the same as those in the first embodiment.
specific Embodiment approach 3
[0041] Specific implementation mode three: combination Figure 1 to Figure 3 Describe this embodiment, in the eighth step described in this embodiment, the set balance pressure P 1 Equal to 0.3 ~ 0.5MPa. The undisclosed technical features in this embodiment are the same as those in the first or second specific embodiment.
PUM
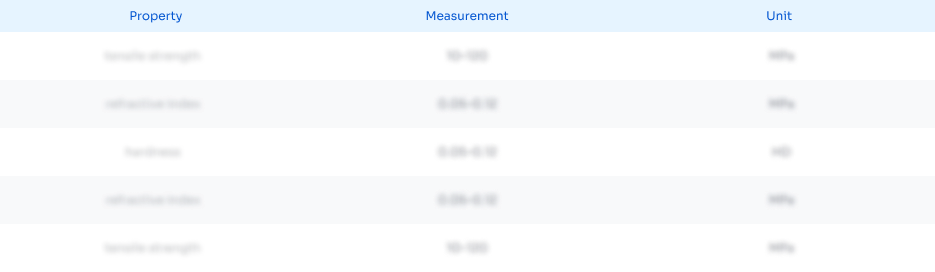
Abstract
Description
Claims
Application Information

- R&D
- Intellectual Property
- Life Sciences
- Materials
- Tech Scout
- Unparalleled Data Quality
- Higher Quality Content
- 60% Fewer Hallucinations
Browse by: Latest US Patents, China's latest patents, Technical Efficacy Thesaurus, Application Domain, Technology Topic, Popular Technical Reports.
© 2025 PatSnap. All rights reserved.Legal|Privacy policy|Modern Slavery Act Transparency Statement|Sitemap|About US| Contact US: help@patsnap.com