Hot working treatment technology for PPS modified materials
A treatment process and modified material technology, which is applied in the field of PPS modified material preparation, can solve the problems of PPS material containing air bubbles, PPS material impurity content exceeding the standard, and quality not up to standard, etc., to achieve uniform melting, reasonable thermal processing process, and improved quality effect
- Summary
- Abstract
- Description
- Claims
- Application Information
AI Technical Summary
Problems solved by technology
Method used
Image
Examples
Embodiment 1
[0037] The PPS material is granulated through the special PPS material, and the granulated PPS material is sieved through the sieving mechanism to screen out the PPS material whose internal size is too large.
[0038] Rinse the sieved good PPS pellets twice with clean water, dehydrate the rinsed PPS pellets, send the dehydrated PPS pellets to an oven at 80°C for 5 minutes, and send the dried PPS materials into Heat in an oven at 250°C for 10 minutes.
[0039] The softened PPS material is sent to a furnace at 350°C for melting, and at the same time, it is stirred with a stirring paddle. The PPS material is stirred for 5 minutes after melting, and the melted PPS material is sent to a furnace at 320°C for constant temperature storage.
Embodiment 2
[0041] The PPS material is granulated through the special PPS material, and the granulated PPS material is sieved through the sieving mechanism to screen out the PPS material whose internal size is too large.
[0042] Rinse the sieved good PPS pellets with clean water for 3 times, dehydrate the rinsed PPS pellets, send the dehydrated PPS pellets to an oven at 82°C for 6 minutes, and send the dried PPS materials into Heat in an oven at 255°C for 10 minutes.
[0043] The softened PPS material is sent to a furnace at 360°C for melting, and at the same time, it is stirred with a stirring paddle. The PPS material is stirred for 5min-6min after melting, and the melted PPS material is sent to a furnace at 320°C for constant temperature storage.
[0044] Thermal Processing Data Sheet of PPS Modified Materials
[0045] Number of washes baking temperature baking time softening temperature melting temperature 2 80℃ 5 250℃ 350℃ 3 82℃ 6 255℃ 360℃
[...
PUM
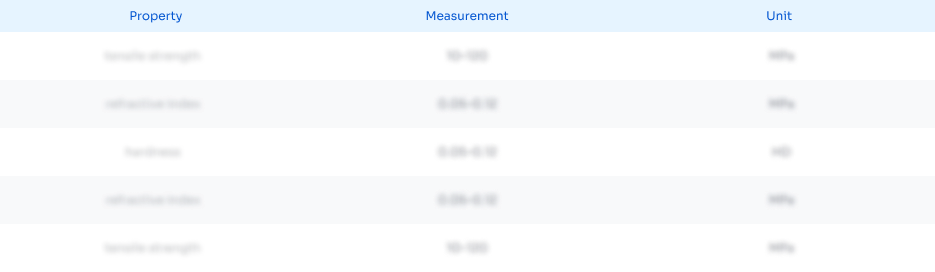
Abstract
Description
Claims
Application Information

- R&D Engineer
- R&D Manager
- IP Professional
- Industry Leading Data Capabilities
- Powerful AI technology
- Patent DNA Extraction
Browse by: Latest US Patents, China's latest patents, Technical Efficacy Thesaurus, Application Domain, Technology Topic, Popular Technical Reports.
© 2024 PatSnap. All rights reserved.Legal|Privacy policy|Modern Slavery Act Transparency Statement|Sitemap|About US| Contact US: help@patsnap.com