Edge sensor for mosaic mirror surface based on interference principle and its working method
A sensor and edge technology, which is applied in the field of contact edge sensors for splicing mirrors, can solve the problems of limited batch size, high price, and impact on measurement accuracy, and achieve the effects of convenient installation, debugging and testing, low installation accuracy requirements, and clear principles
- Summary
- Abstract
- Description
- Claims
- Application Information
AI Technical Summary
Problems solved by technology
Method used
Image
Examples
Embodiment 1
[0035] Embodiment 1, with reference to figure 1 : place a flat crystal 6 on the seam of the concave spherical splicing mirror 7 in the figure or on the two ends (corner points) of the seam (there may be a simple thin pad to avoid contact damage and not affect the measurement and processing), the light source 1 and the collimation The mirror 2 forms a collimated parallel beam, and the parallel beam enters the optical path through the semi-transparent and half-reflective prism 3 outside the optical path and then vertically incident on the flat crystal 6 and the splicing mirror 7, the front surface of the flat crystal 6 is coated with an anti-reflection film, and the rear surface is coated with a part of the reflective part Transmissive film (making the energy of the two reflected light beams that return to the half-reflective prism 3 from the flat crystal 6 close at last to form equal-thickness interference fringes), the interference fringes pass through the microscope 4, are ima...
Embodiment 2
[0036] Embodiment 2, with reference to figure 2 , is basically the same as Embodiment 1, but the splicing mirror surface 8 is a convex spherical or aspheric mirror; the fringes are imaged on the detector 5, and are also image-processed by a computer to obtain the splicing mirror error. The light intensity distribution of the equal-thickness interference fringes in this example is slightly different from that in Example 1, but the processing method is the same, by fitting the light intensity distribution or by changing the image center and radius.
Embodiment 3
[0037] Embodiment 3, with reference to image 3 , is basically the same as Embodiment 1 and Embodiment 2, but the splicing mirror surface 10 is a plane mirror, and what is matched to realize equal-thickness interference fringes is a plano-convex lens 9; the parallel light beam enters the optical path through the semi-transparent and half-reflective prism 3 outside the optical path and then enters the optical path vertically To the plano-convex lens 9 and the splicing mirror surface 10, the front surface of the plano-convex lens 9 is plated with an anti-reflection film, the rear surface is plated with a partly reflective part of the transmissive film (making the energy of two beams of reflected light beams that are returned to the semi-transparent half-reflective prism 3 from the plano-convex lens 9 approach at last, Form equal-thickness interference fringes), the fringes are imaged on the detector 5, and are also image-processed by a computer to obtain stitching mirror errors. ...
PUM
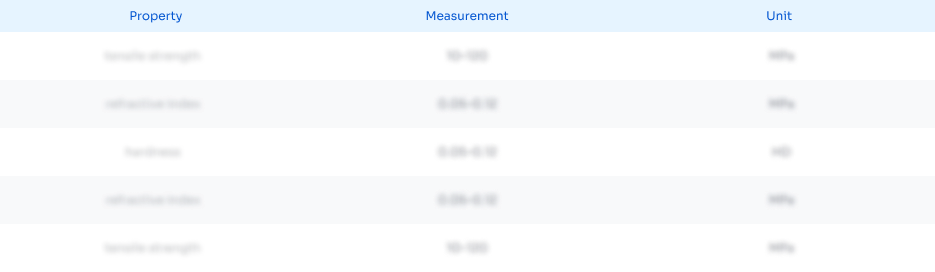
Abstract
Description
Claims
Application Information

- Generate Ideas
- Intellectual Property
- Life Sciences
- Materials
- Tech Scout
- Unparalleled Data Quality
- Higher Quality Content
- 60% Fewer Hallucinations
Browse by: Latest US Patents, China's latest patents, Technical Efficacy Thesaurus, Application Domain, Technology Topic, Popular Technical Reports.
© 2025 PatSnap. All rights reserved.Legal|Privacy policy|Modern Slavery Act Transparency Statement|Sitemap|About US| Contact US: help@patsnap.com