Sintering flue gas SCR denitration and vapor removal system and technology
A technology for sintering flue gas and denitrification, which is applied to the SCR denitration and dewhitening system and process field of sintering flue gas, can solve the problems of inability to meet environmental standards, low saturated flue gas temperature, atmospheric visual pollution, etc., and achieve good dust removal and dewhitening effects. , the effect of saving energy and low operating cost
- Summary
- Abstract
- Description
- Claims
- Application Information
AI Technical Summary
Problems solved by technology
Method used
Image
Examples
Embodiment Construction
[0057] The present invention will be further described in detail below in conjunction with the accompanying drawings and embodiments.
[0058] see Figure 1-Figure 4 , a sintering flue gas SCR denitrification and whitening system related to the present invention, comprising a flue gas condensation dewhitening demisting and dedusting tower 1, a heat exchange device 2, a hot blast stove 4, an ammonia water evaporator 5, a dilution fan 6, and an ammonia spraying grid 7. The SCR denitrification reaction device 8 and the smoke exhaust device 10, the first main flue 11 is connected between the raw flue gas inlet 21 at the lower part of the heat exchange device 2 and the gas outlet of the flue gas condensation, whitening, fogging and dust removal tower 1 , the second main flue 12 is connected between the original flue gas outlet 22 on the upper part of the heat exchange device 2 and the air inlet of the SCR denitrification reaction device 8, and the clean flue gas inlet 23 on the upp...
PUM
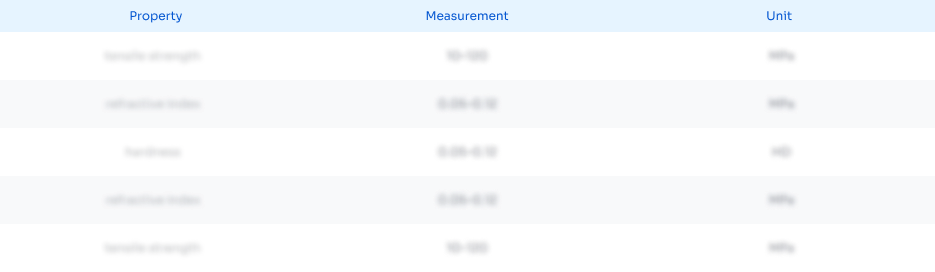
Abstract
Description
Claims
Application Information

- Generate Ideas
- Intellectual Property
- Life Sciences
- Materials
- Tech Scout
- Unparalleled Data Quality
- Higher Quality Content
- 60% Fewer Hallucinations
Browse by: Latest US Patents, China's latest patents, Technical Efficacy Thesaurus, Application Domain, Technology Topic, Popular Technical Reports.
© 2025 PatSnap. All rights reserved.Legal|Privacy policy|Modern Slavery Act Transparency Statement|Sitemap|About US| Contact US: help@patsnap.com