Preparation method of shock-resisting, heat-preservation and sound-proofing board
A technology for thermal insulation, sound insulation and impact resistance, which is applied in thermal insulation, sound insulation, building components, etc., can solve the problems of poor thermal insulation and sound insulation performance, low impact resistance, etc., to increase consumption, improve sound insulation and noise reduction performance, and improve dynamic mechanics. effect of nature
- Summary
- Abstract
- Description
- Claims
- Application Information
AI Technical Summary
Problems solved by technology
Method used
Examples
Embodiment 1
[0037] Preparation of waste circuit board powder:
[0038] Collect the discarded circuit boards and put them into a shredder, crush them for 3 hours, put the crushed circuit boards into an electric vibrating screen machine, use 30 mesh, 220 mesh, 320 mesh and 400 mesh sieve layers in sequence, sieve layer by layer for 30 minutes, collect The sifted powder is the waste circuit board powder, which is reserved;
[0039] Preparation of homemade mineral fibers:
[0040] Mix zirconia ball milling beads and montmorillonite according to the mass ratio of ball to material at 20:1, put them into a ball mill jar, grind and pulverize for 3 hours, pass through a 100-mesh sieve, collect the sieved powder, and put the sifted powder into a high-temperature resistance furnace , heated up to 1600°C, and after melting at high temperature for 1 hour, pour the molten liquid into the wire drawing bushing and draw it into shape to obtain self-made mineral fibers for future use;
[0041] Preparatio...
Embodiment 2
[0050] Preparation of waste circuit board powder:
[0051] Collect the discarded circuit boards and put them into a shredder, crush them for 4 hours, put the crushed circuit boards into an electric vibrating screen machine, use 30 mesh, 220 mesh, 320 mesh and 400 mesh sieve layers in sequence, sieve layer by layer for 35 minutes, collect The sifted powder is the waste circuit board powder, which is reserved;
[0052] Preparation of homemade mineral fibers:
[0053] Mix zirconia ball milling beads and montmorillonite according to the mass ratio of ball to material at 20:1, put them into a ball mill jar, grind and pulverize for 4 hours, pass through a 100-mesh sieve, collect the sieved powder, and put the sifted powder into a high-temperature resistance furnace , heated up to 1650°C, and after melting at high temperature for 1.5 hours, pour the molten liquid into the wire drawing bushing for drawing and forming, and obtain self-made mineral fibers for future use;
[0054] Prep...
Embodiment 3
[0063] Preparation of waste circuit board powder:
[0064] Collect waste circuit boards and put them into a shredder, crush them for 5 hours, put the crushed circuit boards into an electric vibrating sieve machine, use 30 mesh, 220 mesh, 320 mesh and 400 mesh sieve layers in sequence, sieve layer by layer for 40 minutes, collect The sifted powder is the waste circuit board powder, which is reserved;
[0065] Preparation of homemade mineral fibers:
[0066] Mix zirconia ball milling beads and montmorillonite according to the mass ratio of ball to material at 20:1, put them into a ball mill jar, grind and pulverize them for 5 hours, pass through a 100-mesh sieve, collect the sieved powder, and put the sifted powder into a high-temperature resistance furnace , heated up to 1700°C, and after melting at high temperature for 2 hours, pour the molten liquid into the wire drawing bushing and draw it into shape to obtain self-made mineral fibers for future use;
[0067] Preparation o...
PUM
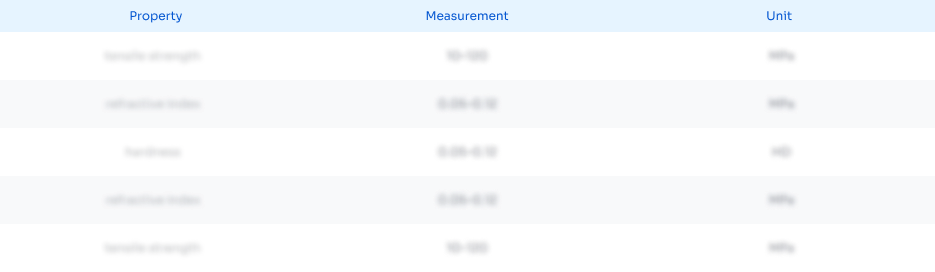
Abstract
Description
Claims
Application Information

- Generate Ideas
- Intellectual Property
- Life Sciences
- Materials
- Tech Scout
- Unparalleled Data Quality
- Higher Quality Content
- 60% Fewer Hallucinations
Browse by: Latest US Patents, China's latest patents, Technical Efficacy Thesaurus, Application Domain, Technology Topic, Popular Technical Reports.
© 2025 PatSnap. All rights reserved.Legal|Privacy policy|Modern Slavery Act Transparency Statement|Sitemap|About US| Contact US: help@patsnap.com