CeO2-SnO2 compound oxide catalyst and production method and application thereof
A technology of composite oxides and catalysts, applied in metal/metal oxide/metal hydroxide catalysts, physical/chemical process catalysts, chemical instruments and methods, etc., can solve problems such as poor activity, achieve good sulfur resistance, The effect of high catalytic efficiency
- Summary
- Abstract
- Description
- Claims
- Application Information
AI Technical Summary
Problems solved by technology
Method used
Image
Examples
Embodiment 1
[0025] Embodiment 1: take by weighing 7.5697g Ce(NO3) 3.6H2O and 4.64g SnCl4.5H2O, add 17.44ml and 13.24ml deionized water to dissolve respectively, after stirring to colorless transparent solution, two kinds of solutions are joined in A mixed solution was obtained in a beaker. Put the beaker of the mixed solution on the magnetic stirrer, pour the 0.5mol / L ammonia solution prepared in advance into the separatory funnel, and continuously add it to the mixed solution by dropping, while keeping the magnetic stirrer at room temperature Rotate at a constant speed. At the same time, keep checking the pH value of the mixed solution with PH test paper until the pH is about 10, stop adding the ammonia solution, turn off the magnetic stirrer, and leave the mixed solution for 24 hours. Wash and filter with deionized water until no chloride ions are detected in the mixed solution with silver nitrate solution. The resulting sample was continuously dried in an oven for 11 hours at 120°C t...
Embodiment 2
[0026] Embodiment 2: take by weighing 7.5697g Ce(NO3) 6H2O, SnCl4.5H2O and 12.93g citric acid (CA) of 7.5697g, add the deionized water of 17.44ml, 13.24ml and 62.8ml respectively, stir until The three substances were dissolved to ensure that the molar ratio of metal ions and citric acid was 1:1. The three solutions were poured into a 500ml beaker, stirred for 12 hours, then placed in a water bath and heated and stirred at 80°C to continuously evaporate the water until a highly thick gel was formed. The resulting gel was dried in an oven for 11 hours at a temperature of 110°C to obtain a catalyst precursor, and then the sample was taken out and transferred to a crucible and baked in a muffle furnace at a temperature of 500°C After 4 hours, it was naturally cooled to room temperature, and finally the CeO2-SnO2 composite oxide SCR catalyst prepared by the sol-gel method was obtained. The samples were sieved and pressed into tablets, and 40-60 mesh catalyst particles were sieved ...
Embodiment 3
[0027] Embodiment 3: take by weighing 7.5697g of Ce(NO3) 3.6H2O and 4.64g of SnCl4.5H2O, the weighed Ce(NO3)3.6H2O and SnCl4.5H2O are poured into agate mortar and ground, then poured into Pulverize in a ball mill for 3 hours, put the pulverized mixture into a crucible, and roast it in a muffle furnace for 4 hours at a temperature of 500°C, then cool naturally to room temperature, and finally obtain CeO2 prepared by a solid-state method -SnO2 composite oxide SCR catalyst. The samples were sieved and pressed into tablets, and catalyst particles of 40-60 meshes were screened out for activity testing.
PUM
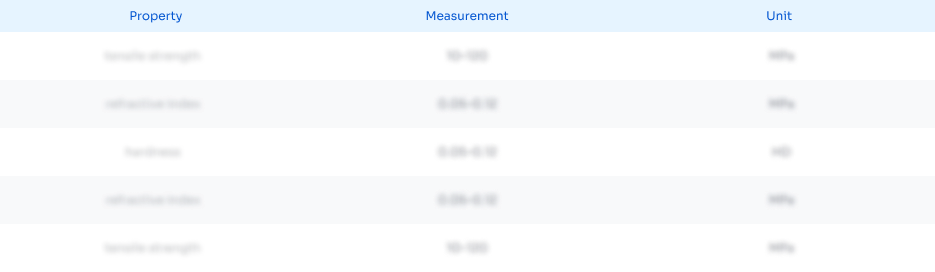
Abstract
Description
Claims
Application Information

- R&D
- Intellectual Property
- Life Sciences
- Materials
- Tech Scout
- Unparalleled Data Quality
- Higher Quality Content
- 60% Fewer Hallucinations
Browse by: Latest US Patents, China's latest patents, Technical Efficacy Thesaurus, Application Domain, Technology Topic, Popular Technical Reports.
© 2025 PatSnap. All rights reserved.Legal|Privacy policy|Modern Slavery Act Transparency Statement|Sitemap|About US| Contact US: help@patsnap.com