Method for quick repair of nickel-base superalloy turbine disk at the end of service
A nickel-based superalloy and turbine disc technology, which is applied in the field of rapid repair of nickel-based superalloy turbine discs at the end of service, to achieve the effect of reducing the number density, simple operation and restoring mechanical properties
- Summary
- Abstract
- Description
- Claims
- Application Information
AI Technical Summary
Problems solved by technology
Method used
Image
Examples
Embodiment 1
[0030] In this embodiment, pulse current treatment is performed on a small-sized aged superalloy turbine disk. Specific steps are as follows:
[0031] Step 1: Take 25mm×3.5mm×0.6mm aged turbine disk material, and sand the surface with 600, 1500, 2000 grit sandpaper in turn until there are no visible defects to the naked eye to ensure good contact with the pulse electrode.
[0032] Step 2: Determine the pulse processing parameters. The parameter range of the pulse current is set, and the parameters of the pulse current are determined to be 40Hz, 20μs, 3000A, and the action time is 10h.
[0033] The third step: pulse current processing. Fix the polished turbine disc on the output end of the pulse power supply with a clamp, and perform pulse current treatment on it for 20 min at room temperature.
[0034]The fourth step: observe the distribution of brittle topological close-packed phase by metallographic microscope. A 3.5mm×5mm×0.6mm slice was made from any position of the ag...
Embodiment 2
[0037] In this embodiment, pulse current treatment is performed on a small-sized aged superalloy turbine disk. Specific steps are as follows:
[0038] Step 1: Take 25mm×3.5mm×0.6mm aged turbine disk material, and sand the surface with 600, 1500, 2000 grit sandpaper in turn until there are no visible defects to the naked eye to ensure good contact with the pulse electrode.
[0039] Step 2: Determine the pulse processing parameters. The parameter range of the pulse current is set, and the parameters of the pulse current are determined to be 400Hz, 60μs, 200A, and the action time is 10min.
[0040] The third step: pulse current processing. Fix the small-sized turbine disk after grinding on the output end of the pulse power supply with a clamp, and perform pulse current treatment on it for 10 min at room temperature.
[0041] The fourth step: observe the distribution of brittle topological close-packed phase by metallographic microscope. A 3.5mm×5mm×0.6mm slice was made from a...
Embodiment 3
[0044] In this embodiment, pulse current treatment is performed on a small-sized aged superalloy turbine disk. Specific steps are as follows:
[0045] Step 1: Take 25mm×3.5mm×0.6mm aged turbine disk material, and sand the surface with 600, 1500, 2000 grit sandpaper in turn until there are no visible defects to the naked eye to ensure good contact with the pulse electrode.
[0046] Step 2: Determine the pulse processing parameters. The parameter range of the pulse current is set, and the parameters of the pulse current are determined to be 30000Hz, 75μs, 150A, and the action time is 5min.
[0047] The third step: pulse current processing. The small-sized turbine disk after grinding was fixed on the output end of the pulse power supply with a clamp, and it was treated with pulse current for 5 minutes at room temperature.
[0048] The fourth step: observe the distribution of brittle topological close-packed phase by metallographic microscope. A 3.5mm×5mm×0.6mm slice was made ...
PUM
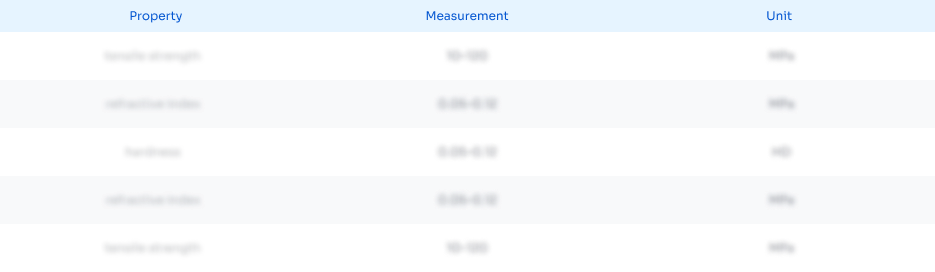
Abstract
Description
Claims
Application Information

- Generate Ideas
- Intellectual Property
- Life Sciences
- Materials
- Tech Scout
- Unparalleled Data Quality
- Higher Quality Content
- 60% Fewer Hallucinations
Browse by: Latest US Patents, China's latest patents, Technical Efficacy Thesaurus, Application Domain, Technology Topic, Popular Technical Reports.
© 2025 PatSnap. All rights reserved.Legal|Privacy policy|Modern Slavery Act Transparency Statement|Sitemap|About US| Contact US: help@patsnap.com