On-line monitoring method of tightly sealed labyrinth gap and leakage flow
A technology for sealing the grate teeth and leakage flow, which is applied in the field of aero-engines, can solve the problems of not being able to obtain the cooling air volume of the hot-end components in real time, and can not perform real-time measurement, so as to save experiment costs, reduce measurements, and save experiment time.
- Summary
- Abstract
- Description
- Claims
- Application Information
AI Technical Summary
Problems solved by technology
Method used
Image
Examples
Embodiment 1
[0070] Under the condition of fixing the structural parameters of the studied grate tooth, such as figure 2 As shown, the pressure measuring points are arranged in the 3 sections before the rotating grate to obtain the total pressure before the rotating grate, and because the speed of the 3 section is low, the static pressure of the 3 section is used instead of the total pressure, after the rotating grate 4 Pressure measuring points are arranged on the section to obtain the static pressure of the 4 sections to obtain the pressure ratio π of the rotating grate at different speeds. The total temperature of the inlet and outlet, so as to obtain the windage temperature rise ΔT of the rotating grate * .
[0071] In addition, the change of the rotating speed will change the working clearance of the rotating grate, which is mainly caused by the size change of both the ring casing and the rotating grate. A laser displacement sensor is placed at the position to monitor the dimension...
Embodiment 2
[0073] In the case of fixing the geometric parameters of the sealing grate, assuming the inlet and outlet pressure and temperature of the rotating grate, the corresponding sealing clearance c and leakage flow m of the rotating grate are obtained and compared with the experimental data, finally the rotating grate Deviation of sealing gap c and leakage flow m.
[0074] The geometric parameters of the sealed grate are: radius R=293.7mm, tooth height H=6mm, tooth pitch P=6mm, tooth top width t=0.45mm, forward inclination α=15°, back inclination β=30° .
[0075] Table 3 shows the deviation comparison between the experimental leakage flow rate and grate tooth sealing clearance and the calculated leakage flow rate and grate tooth sealing clearance under different working conditions. It can be seen from the table that the fitted flow coefficient and fitted dimensionless temperature ratio obtained by the estimation method have a small deviation from the experimental flow coefficient a...
PUM
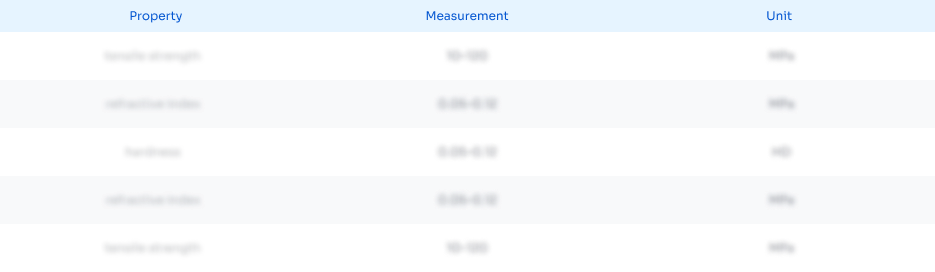
Abstract
Description
Claims
Application Information

- Generate Ideas
- Intellectual Property
- Life Sciences
- Materials
- Tech Scout
- Unparalleled Data Quality
- Higher Quality Content
- 60% Fewer Hallucinations
Browse by: Latest US Patents, China's latest patents, Technical Efficacy Thesaurus, Application Domain, Technology Topic, Popular Technical Reports.
© 2025 PatSnap. All rights reserved.Legal|Privacy policy|Modern Slavery Act Transparency Statement|Sitemap|About US| Contact US: help@patsnap.com