Method for preparing spinel structure cobalt aluminate pigment by solution combustion method
A technology of spinel structure and solution combustion, applied in chemical instruments and methods, preparation of alkali metal aluminate/alumina/aluminum hydroxide, cobalt compounds, etc., can solve complicated operation, high cost, and limited use of high-quality pigments range and other issues, to achieve the effect of wide application and high yield
- Summary
- Abstract
- Description
- Claims
- Application Information
AI Technical Summary
Problems solved by technology
Method used
Image
Examples
Embodiment 1
[0034] Example 1: Spinel Al 2 o 3 preparation of
[0035] Weigh 0.7503g Al(NO 3 )·9H 2 O (2mmol) and 0.1501g C 2 h 5 NO 2 (glycine 2mmol) in a 100mL quartz beaker, then add 10mL distilled water and stir thoroughly to dissolve it completely. Adjust the temperature of the flat furnace to 400°C, place the prepared solution on the flat furnace, and burn the solution after evaporation and concentration (about 5 minutes in the whole process) to generate a gray foamy precursor. Put the precursor into a crucible, heat up to 900°C in a muffle furnace and calcinate for 4 hours, then cool to room temperature, the product is a white powder, see the physical photo figure 1 .
[0036] The scanning electron micrograph of the product of the present embodiment is as figure 2 As shown, the XRD diffraction pattern and the standard spectrum line contrast figure are as follows image 3 As shown, the X-ray diffraction pattern and the spinel structure of γ-Al 2 o 3 The peak position and...
Embodiment 2
[0039] Example 2: Spinel Co 0.1 Al 2 o 3.1 preparation of
[0040] Weigh 0.0291g Co(NO 3 ) 2 ·6H 2 O (0.1mmol), 0.7503g Al (NO 3 )·9H 2 O (2mmol) and 0.1501g C 2 h 5 NO 2 (glycine 2mmol) in a 100mL quartz beaker, then add 10mL distilled water and stir thoroughly to dissolve it completely. Adjust the temperature of the flat furnace to 400°C, place the prepared solution on the flat furnace, and burn the solution after evaporation and concentration (about 5 minutes in the whole process) to generate a gray foamy precursor. The precursor was put into a crucible and heated to 900°C in a muffle furnace for calcination for 4 hours, then cooled to room temperature, and the product was a light blue powder.
[0041] After the X-ray diffraction pattern of the product of this embodiment is indexed, the unit cell parameters are consistent with the spinel structure, and there is no diffraction peak of the impurity phase. The product was determined to be in the spinel phase. The ...
Embodiment 3
[0044] Example 3: Spinel Co 0.2 Al 2 o 3.2 preparation of
[0045] Weigh 0.0582g Co(NO 3 ) 2 ·6H 2 O (0.2mmol), 0.7503g Al (NO 3 )·9H 2 O (2mmol) and 0.1501g C 2 h 5 NO 2 (glycine 2mmol) in a 100mL quartz beaker, then add 10mL distilled water and stir thoroughly to dissolve it completely. Adjust the temperature of the flat furnace to 400°C, place the prepared solution on the flat furnace, and burn the solution after evaporation and concentration (about 5 minutes in the whole process) to generate a gray foamy precursor. The precursor was put into a crucible and heated to 900°C in a muffle furnace for calcination for 4 hours, then cooled to room temperature, and the product was a light blue powder. real photo see figure 1 (Note: Since the Patent Office does not support color drawings, the figure 1 In the photos shown, each product shows different degrees of gray, and the actual removal of Al 2 o 3 In addition to being white, the rest of the products are blue in va...
PUM
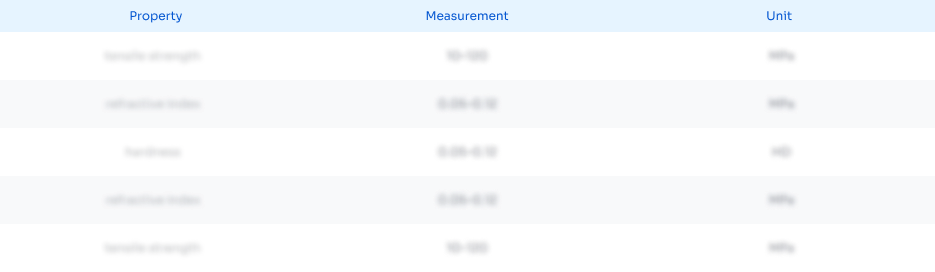
Abstract
Description
Claims
Application Information

- Generate Ideas
- Intellectual Property
- Life Sciences
- Materials
- Tech Scout
- Unparalleled Data Quality
- Higher Quality Content
- 60% Fewer Hallucinations
Browse by: Latest US Patents, China's latest patents, Technical Efficacy Thesaurus, Application Domain, Technology Topic, Popular Technical Reports.
© 2025 PatSnap. All rights reserved.Legal|Privacy policy|Modern Slavery Act Transparency Statement|Sitemap|About US| Contact US: help@patsnap.com