Alloy fused mold precision casting model material and preparation method and application thereof
An investment precision casting and model material technology, applied in the field of alloy investment casting model materials, can solve the problems of affecting product delivery, excessive model shrinkage, insufficient stability, etc., to achieve enhanced mechanical properties, high surface finish, and difficult deformation effect
- Summary
- Abstract
- Description
- Claims
- Application Information
AI Technical Summary
Problems solved by technology
Method used
Examples
Embodiment 1
[0032] A method for preparing a titanium alloy investment casting model material for an aero-engine, the steps of which are:
[0033] 1. Selection of raw materials: 45 parts of granular white solid semi-refined paraffin wax, 15 parts of super-grade rosin, 5 parts of linear low-density polyethylene, and a wax material configuration barrel of Φ300×h500.
[0034] 2. Configuration sequence:
[0035] (1) When the configuration barrel is preheated to 40°C, add the paraffin to melt the paraffin;
[0036] (2) When continuing to heat to 70°C, add the super-grade rosin and stir for 10 minutes to fully dissolve the super-grade rosin and paraffin;
[0037] (3) Add polyethylene when heating to 130°C, then stop heating after heating to 160°C, and stir for 30 minutes to make linear low-density polyethylene fully compatible with natural resin and wax; let stand and cool to room temperature to obtain .
Embodiment 2
[0039] A method for preparing a titanium alloy investment casting model material for an aero-engine, the steps of which are:
[0040] 1. Selection of raw materials: 65 parts of granular white solid semi-refined paraffin wax, 30 parts of super-grade rosin, 2 parts of linear low-density polyethylene, and a wax material configuration barrel of Φ300×h500.
[0041] 2. Configuration sequence:
[0042] (1) Add the paraffin when the configuration barrel is preheated to 45°C to melt the paraffin;
[0043] (2) When continuing to heat to 70°C, add the super-grade rosin and stir for 10 minutes to fully dissolve the super-grade rosin and paraffin;
[0044] (3) Add polyethylene when heating to 135°C, then stop heating after heating to 170°C, and stir for 40 minutes to make linear low-density polyethylene fully compatible with natural resin and wax; let stand and cool to room temperature to obtain .
Embodiment 3
[0046] A method for preparing a titanium alloy investment casting model material for an aero-engine, the steps of which are:
[0047]1. Selection of raw materials: 48 parts of granular white solid semi-refined paraffin wax, 24 parts of super-grade rosin, 5 parts of linear low-density polyethylene, and a wax material configuration barrel of Φ300×h500.
[0048] 2. Configuration sequence:
[0049] (1) When the configuration barrel is preheated to 40°C, add the paraffin to melt the paraffin;
[0050] (2) When continuing to heat to 75°C, add the super-grade rosin and stir for 5 minutes, so that the super-grade rosin and paraffin are fully compatible;
[0051] (3) Add polyethylene when heating to 130°C, then stop heating after heating to 160°C, and stir for 30 minutes to make linear low density polyethylene fully compatible with natural resin and wax; then continue heating to 180°C and keep warm for 2 minutes Then stop heating, let stand, cool to room temperature, that is.
PUM
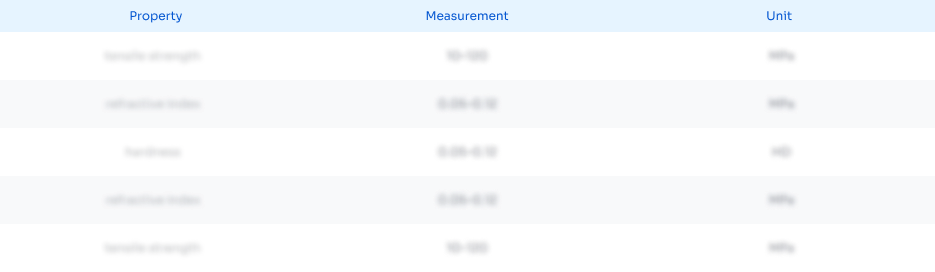
Abstract
Description
Claims
Application Information

- R&D Engineer
- R&D Manager
- IP Professional
- Industry Leading Data Capabilities
- Powerful AI technology
- Patent DNA Extraction
Browse by: Latest US Patents, China's latest patents, Technical Efficacy Thesaurus, Application Domain, Technology Topic, Popular Technical Reports.
© 2024 PatSnap. All rights reserved.Legal|Privacy policy|Modern Slavery Act Transparency Statement|Sitemap|About US| Contact US: help@patsnap.com