Manufacturing process of high-wear-resistance gear
A technology with high wear resistance and manufacturing process, applied in the direction of manufacturing tools, wheels, furnace types, etc., it can solve the problems of low uniformity of the internal structure of the metal, insufficient filling, and excessive forming force, and achieve full filling of the metal. Internal structure uniformity, internal deformation uniformity, the effect of improving bending fatigue strength and contact fatigue strength
- Summary
- Abstract
- Description
- Claims
- Application Information
AI Technical Summary
Problems solved by technology
Method used
Examples
Embodiment 1
[0061] A manufacturing process for highly wear-resistant gears, the parts by weight of each component in the formula are as follows:
[0062] 95 parts of iron,
[0063] Carbon 0.38 parts,
[0064] 0.05 parts of titanium,
[0065] 0.04 parts of cerium,
[0066] Lanthanum 0.04 parts,
[0067] Chromium 0.80 parts,
[0068] Silicon 0.15 parts,
[0069] Manganese 1.8 parts;
[0070] The specific manufacturing steps are as follows:
[0071] Step 1, blanking:
[0072] Heating the steel ingot with the above components to 950°C, and successively go through the processes of jaw pressing, chamfering, and spouting;
[0073] Step 2, repeated forging:
[0074] Put the billet prepared in step 1 into the forging press for forging, adopt the forging method of extreme widening, that is, make the deformation direction limit deformation in one direction during forging; heat the forged billet to 950 °C again, and forge again, Repeat this several times;
[0075] Step three, tempering:
...
Embodiment 2
[0088] A manufacturing process for highly wear-resistant gears, the parts by weight of each component in the formula are as follows:
[0089] Iron 100 parts,
[0090] Carbon 0.43 parts,
[0091] 0.07 parts of titanium,
[0092] 0.06 parts of cerium,
[0093] Lanthanum 0.06 parts,
[0094] Chromium 1.10 parts,
[0095] Silicon 0.35 parts,
[0096] Manganese 2.3 parts;
[0097] The specific manufacturing steps are as follows:
[0098] Step 1, blanking:
[0099] Heat the steel ingot with the above components to 1200°C, and then make the billet through the processes of jaw pressing, chamfering and spouting in sequence;
[0100] Step 2, repeated forging:
[0101] Put the billet prepared in step 1 into the forging press for forging, adopt the extreme widening forging method, that is, make the deformation direction limit deformation in one direction during forging; heat the forged billet to 1200 °C again, and forge again, Repeat this several times;
[0102] Step three, tem...
Embodiment 3
[0115] A manufacturing process for highly wear-resistant gears, the parts by weight of each component in the formula are as follows:
[0116] 96 parts of iron,
[0117] Carbon 0.39 parts,
[0118] 0.06 parts of titanium,
[0119] 0.05 parts of cerium,
[0120] Lanthanum 0.05 parts,
[0121] Chromium 0.90 parts,
[0122] Silicon 0.25 parts,
[0123] Manganese 1.9 parts;
[0124] The specific manufacturing steps are as follows:
[0125] Step 1, blanking:
[0126] Heat the steel ingot with the above components to 1100°C, and sequentially go through the processes of jaw pressing, chamfering, and spouting;
[0127] Step 2, repeated forging:
[0128] Put the billet prepared in step 1 into the forging press for forging, adopt the forging method of extreme widening, that is, make the deformation direction limit deformation in one direction during forging; heat the forged billet to 1100 °C again, and forge again, Repeat this several times;
[0129] Step three, tempering:
...
PUM
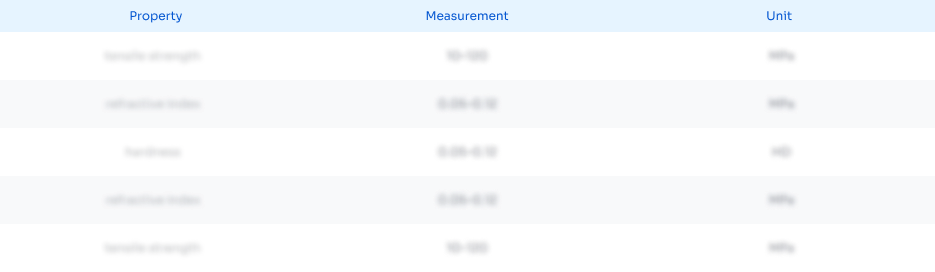
Abstract
Description
Claims
Application Information

- R&D
- Intellectual Property
- Life Sciences
- Materials
- Tech Scout
- Unparalleled Data Quality
- Higher Quality Content
- 60% Fewer Hallucinations
Browse by: Latest US Patents, China's latest patents, Technical Efficacy Thesaurus, Application Domain, Technology Topic, Popular Technical Reports.
© 2025 PatSnap. All rights reserved.Legal|Privacy policy|Modern Slavery Act Transparency Statement|Sitemap|About US| Contact US: help@patsnap.com