High-temperature stable precoated sand
A high-temperature stable, coated sand technology, used in casting molds, cores, casting and molding equipment, etc., can solve the problems of low high-temperature compressive strength, agglomeration, and shelling of coated sand, and improve compressive performance, Improve the dispersion effect and promote the effect of brittle-ductile transition
- Summary
- Abstract
- Description
- Claims
- Application Information
AI Technical Summary
Problems solved by technology
Method used
Examples
preparation example Construction
[0034] The preparation method of stable modified material A comprises the steps:
[0035] S1. According to the weight fraction, take 20~35 parts of polylactic acid, 2~5 parts of diethanolamine, 1~3 parts of adhesive, 8~13 parts of lanthanum stearate in a mortar and grind at 350~550r / min for 1~3h , to get the grinding material, take the grinding material and mix it in a mixer at 120~140°C for 15~25min, discharge the material, and cool it to room temperature naturally to get the mixing material, take the mixing material according to the mass ratio of 1:5~8 and add it for impregnation mixed liquid, ultrasonically treated in an ultrasonic cleaner at a frequency of 50~65kHz for 12~20min, discharged, filtered, and the collected filter cake was washed with water for 3~5 times, then dried in an oven at 80~100°C to constant weight to obtain a filler;
[0036] S2. At 20~45°C, take bamboo charcoal fiber according to the mass ratio of 8:2~5:1, add N-methylpyrrolidone and calcium stearate ...
Embodiment 1
[0040] Impregnation solution: Mix dopamine hydrochloride and ammonium chloride solution with a mass fraction of 12% at a mass ratio of 1:6 to obtain an impregnation solution.
[0041] Adhesive: Mix cobalt oxide, nickel oxide, and fluorosilicone at a mass ratio of 1:2:3 to obtain an adhesive.
[0042] Additives: Mix epoxidized soybean oil and pentaerythritol in a mass ratio of 3:1 to obtain additives.
[0043] Nano-materials: Mix nano-titanium dioxide, nano-iron powder, and nano-silicon dioxide in a mass ratio of 3:1:2 to obtain nano-materials.
[0044] Modified phenolic resin: mix phenol, formaldehyde solution with a mass fraction of 37%, sodium citrate, and ferrocene at a mass ratio of 1:5:0.3:0.01, and reflux at 90°C for 4 hours to obtain a reaction material. Vacuum dehydration to obtain modified phenolic resin.
[0045] Lubricant: Mix calcium stearate and paraffin wax at a mass ratio of 1:2 to obtain a lubricant.
[0046] Toughening agent: Mix polyvinyl acetate and polyv...
Embodiment 2
[0053] Impregnation solution: Mix dopamine hydrochloride and ammonium chloride solution with a mass fraction of 12% at a mass ratio of 1:8 to obtain an impregnation solution.
[0054] Adhesive: Mix cobalt oxide, nickel oxide, and fluorosilicone in a mass ratio of 1:4:3 to obtain an adhesive.
[0055] Additives: Mix epoxidized soybean oil and pentaerythritol in a mass ratio of 5:1 to obtain additives.
[0056] Nano-material: Mix nano-titanium dioxide, nano-iron powder, and nano-silicon dioxide in a mass ratio of 3:1:4 to obtain nano-material.
[0057] Modified phenolic resin: mix phenol, formaldehyde solution with a mass fraction of 37%, sodium citrate, and ferrocene at a mass ratio of 1:7:0.3:0.01, and reflux at 95°C for 6 hours to obtain a reaction material. Vacuum dehydration to obtain modified phenolic resin.
[0058] Lubricant: Mix calcium stearate and paraffin wax at a mass ratio of 1:3 to obtain a lubricant.
[0059] Toughening agent: Mix polyvinyl acetate and polyvin...
PUM
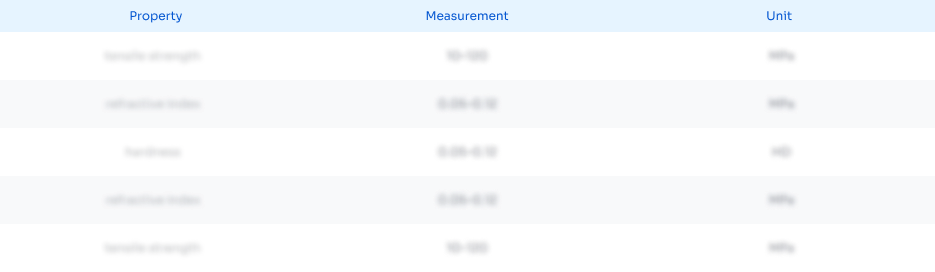
Abstract
Description
Claims
Application Information

- R&D
- Intellectual Property
- Life Sciences
- Materials
- Tech Scout
- Unparalleled Data Quality
- Higher Quality Content
- 60% Fewer Hallucinations
Browse by: Latest US Patents, China's latest patents, Technical Efficacy Thesaurus, Application Domain, Technology Topic, Popular Technical Reports.
© 2025 PatSnap. All rights reserved.Legal|Privacy policy|Modern Slavery Act Transparency Statement|Sitemap|About US| Contact US: help@patsnap.com