Method for modifying surface of ultra-high molecular weight polyethylene fiber
An ultra-high molecular weight, surface modification technology, applied in the direction of single-component polyolefin rayon, chemical characteristics of fibers, textiles and papermaking, etc., can solve the difficulty of preparing modified polyethylene, difficult to control the length of polyethylene segment, It is difficult to obtain and other problems, and achieves the effects of low cost, uniform coverage and easy preparation.
- Summary
- Abstract
- Description
- Claims
- Application Information
AI Technical Summary
Problems solved by technology
Method used
Image
Examples
Embodiment 1
[0029] Add 100 parts of ultra-high molecular weight polyethylene powder with a number average molecular weight of 4.2 million into decahydronaphthalene to form a swelling solution with a mass concentration of 5%, add 2 parts of fatty alcohol polyoxyethylene ether AEO-4 (wherein n=16 , m=4), 2 parts of antioxidant 1076 and 0.2 part of ultraviolet absorber UV326, the swelling temperature is 80° C., and the swelling time is 4 hours to obtain a swelling mixture. Add the swelling mixed liquid to the feed port while stirring, and spin through a twin-screw extruder at an extrusion temperature of 160°C and a spinning temperature of 200°C. The gel silk enters the water bath through the air section of more than ten centimeters, and is immersed in water for 30 seconds to obtain the primary fiber silk. The as-spun fibers were left to stand and dried to remove the solvent, and the drying temperature was 60°C. The prepared as-spun fiber filaments are cleaned and then stretched with ultra-h...
Embodiment 2
[0031] 100 parts of ultra-high molecular weight polyethylene powder with a number average molecular weight of 3.5 million are added to tetralin to form a swelling solution with a mass concentration of 10%, and 2 parts of fatty alcohol polyoxyethylene ether AEO-6 (wherein n=10 , m=6), 2 parts of antioxidant 1076 and 0.3 part of ultraviolet absorber UV531, the swelling temperature is 85° C., and the swelling time is 3 hours to obtain a swelling mixture. Add the swelling mixed liquid to the feed port while stirring, and spin through a twin-screw extruder at an extrusion temperature of 180°C and a spinning temperature of 200°C. The gel filament enters the water bath through the air section of more than ten centimeters, and is immersed in water for 60 seconds to obtain the primary fiber filament. The as-spun fibers were left to stand and dried to remove the solvent, and the drying temperature was 60°C. The prepared as-spun fiber filaments are cleaned and then stretched with ultra-...
Embodiment 3
[0033]The number-average molecular weight is 4,000,000 ultra-high molecular weight polyethylene powder 100 parts join in the tetralin and be configured into the swelling liquid that mass concentration is 6%, add the fatty alcohol polyoxyethylene base ether AEO-8 of 1.5 parts (wherein n= 16, m=8), 1 part of antioxidant 1010 and 0.3 part of ultraviolet absorber UV234, the swelling temperature is 90° C., and the swelling time is 4 hours to obtain a swelling mixture. Add the swelling mixed liquid to the feed port while stirring, and spin through a twin-screw extruder at an extrusion temperature of 160°C and a spinning temperature of 210°C. The gel silk enters the water bath through the air section of more than ten centimeters, and is immersed in water for 30 seconds to obtain the primary fiber silk. The as-spun fibers were left to stand and dried to remove the solvent, and the drying temperature was 60°C. The prepared as-spun fiber filaments are cleaned and then stretched with ul...
PUM
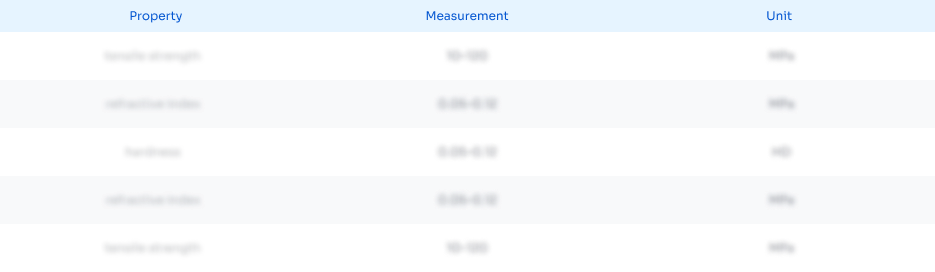
Abstract
Description
Claims
Application Information

- R&D Engineer
- R&D Manager
- IP Professional
- Industry Leading Data Capabilities
- Powerful AI technology
- Patent DNA Extraction
Browse by: Latest US Patents, China's latest patents, Technical Efficacy Thesaurus, Application Domain, Technology Topic, Popular Technical Reports.
© 2024 PatSnap. All rights reserved.Legal|Privacy policy|Modern Slavery Act Transparency Statement|Sitemap|About US| Contact US: help@patsnap.com