Low-phosphorus smelting process for martensitic stainless steel main shaft
A martensitic stainless steel and spindle technology, which is applied to the improvement of process efficiency, furnace type, furnace and other directions, can solve the problems of long smelting cycle, limited production capacity, short process, etc., to reduce the phenomenon of local high phosphorus and improve the composition Uniformity, the effect of improving production efficiency
- Summary
- Abstract
- Description
- Claims
- Application Information
AI Technical Summary
Problems solved by technology
Method used
Examples
Embodiment 1
[0019] Embodiment 1: Taking the 60 tons of molten steel smelting process of this product as an example, the specific implementation of this low phosphorus smelting process is as follows:
[0020] Step 1), electric furnace smelting: the furnace charge is composed of 20t of secondary steel scrap, 10t of steel scrap, 8t of pig iron, 2t of waste ingot mold, 900kg of ferromolybdenum, and 360kg of nickel plate. ~1.5t of lime; After melting, add lime and carbon powder to create foam slag, blow oxygen at a small flow rate, measure temperature T=1590℃ while blowing oxygen while flowing slag, and take samples to detect chemical composition: [C]=1.13%, [P] =0.042%, [Mo]=1.09%, [Ni]=0.75%, [As]=0.008%, [Sn]=0.002%, [Pb]=0.001%, [Sb]=0.002%, [Bi]= 0.001%, continue to blow oxygen during the period, and increase the amount of oxygen blowing to carry out decarburization and dephosphorization operations; temperature measurement T=1652°C, sampling and detection of chemical composition: [C]=0.09...
PUM
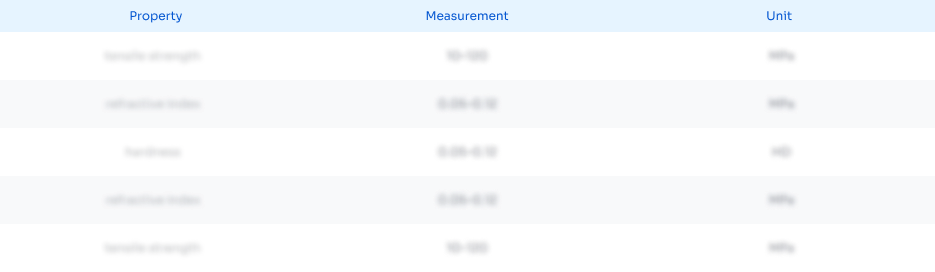
Abstract
Description
Claims
Application Information

- Generate Ideas
- Intellectual Property
- Life Sciences
- Materials
- Tech Scout
- Unparalleled Data Quality
- Higher Quality Content
- 60% Fewer Hallucinations
Browse by: Latest US Patents, China's latest patents, Technical Efficacy Thesaurus, Application Domain, Technology Topic, Popular Technical Reports.
© 2025 PatSnap. All rights reserved.Legal|Privacy policy|Modern Slavery Act Transparency Statement|Sitemap|About US| Contact US: help@patsnap.com