Composite ceramic-phase anti-seepage wear-resistant material produced from polysilicon wastes and used for copper chute
A technology of polysilicon waste and composite ceramics is applied in the field of refractory materials for copper chutes of Ausmelt copper smelting furnaces or aluminum melting furnaces, which can solve the problems of copper liquid slag and water erosion, pollution of the surrounding environment of enterprises, and high maintenance labor intensity, etc. problems, to achieve the effect of reducing porosity, flexible construction, and convenient maintenance
- Summary
- Abstract
- Description
- Claims
- Application Information
AI Technical Summary
Problems solved by technology
Method used
Image
Examples
Embodiment 1
[0037] A method for preparing a composite ceramic phase anti-seepage wear-resistant material for a copper chute produced by polysilicon industrial waste is as follows:
[0038] Step 1. Dry the polysilicon industrial waste sediment first, grind it finely, and put it into a nitriding furnace (N 2 Atmosphere protection furnace) at 1100°C for 24 hours for nitriding treatment to obtain waste slag after nitriding treatment. The waste slag after nitriding treatment includes 55% silicon nitride content and 15% silicon carbide content;
[0039] Step 2: Take 20 parts by weight of waste slag after nitriding treatment, 67 parts by weight of silicon carbide raw material, and 13 parts by weight of binder, put them into a forced mixer for pre-mixing for 10-15 minutes, and add the mixed materials Water, the addition of water is 5% of the total weight of the original material, and the addition of composite additives is 16% of the total weight of the original material; continue to stir for 5-10...
Embodiment 2
[0047] A method for preparing a composite ceramic phase anti-seepage wear-resistant material for a copper chute produced by polysilicon industrial waste is as follows:
[0048] Step 1. Dry the polysilicon industrial waste sediment first, grind it finely, and put it into a nitriding furnace (N 2 Atmosphere protection furnace) at 1300°C for 24 hours for nitriding treatment to obtain waste slag after nitriding treatment. The waste slag after nitriding treatment includes silicon nitride content of 65% and silicon carbide content of 20%;
[0049] Step 2: Take 22 parts by weight of waste slag after nitriding treatment, 66 parts by weight of silicon carbide raw material, and 12 parts by weight of binder, put them into a forced mixer for pre-mixing for 10-15 minutes, and add the mixed materials Water, the addition of water is 8% of the total weight of the original material, and the addition of the composite additive is 12% of the total weight of the original material; continue to stir...
Embodiment 3
[0057] A method for preparing a composite ceramic phase anti-seepage wear-resistant material for a copper chute produced by polysilicon industrial waste is as follows:
[0058] Step 1. Dry the polysilicon industrial waste sediment first, grind it finely, and put it into a nitriding furnace (N 2 Atmosphere protection furnace) at 1100-1300°C for 24 hours for nitriding treatment to obtain waste slag after nitriding treatment. The waste slag after nitriding treatment includes silicon nitride content of 55-65%, silicon carbide content of 15-25% %;
[0059] Step 2: Take 24 parts by weight of waste slag after nitriding treatment, 60 parts by weight of silicon carbide raw material, and 16 parts by weight of binder, put them into a forced mixer for pre-mixing for 10-15 minutes, and add the mixed materials Water, the addition of water is 10% of the total weight of the original material, and the addition of composite additives is 16% of the total weight of the original material; continu...
PUM
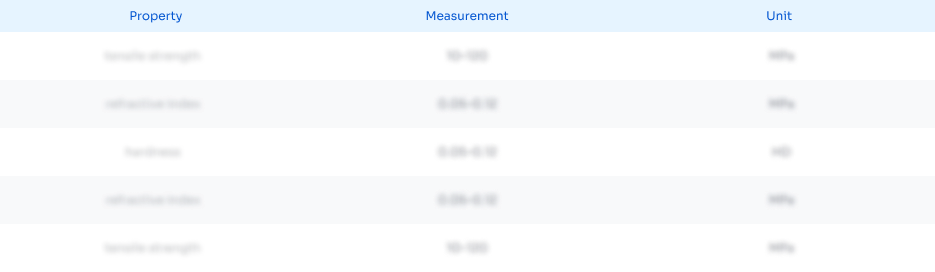
Abstract
Description
Claims
Application Information

- R&D Engineer
- R&D Manager
- IP Professional
- Industry Leading Data Capabilities
- Powerful AI technology
- Patent DNA Extraction
Browse by: Latest US Patents, China's latest patents, Technical Efficacy Thesaurus, Application Domain, Technology Topic, Popular Technical Reports.
© 2024 PatSnap. All rights reserved.Legal|Privacy policy|Modern Slavery Act Transparency Statement|Sitemap|About US| Contact US: help@patsnap.com