Method of utilizing rice bran hydrolysate fermentation to prepare bacterial cellulose
A technology of bacterial cellulose and bacterial cellulose membrane, which is applied in the field of bacterial cellulose preparation, can solve the problems of high raw material production cost, complex process, and environmental pollution, and achieve the effects of environmental protection, simple preparation process, and abundant sources
- Summary
- Abstract
- Description
- Claims
- Application Information
AI Technical Summary
Problems solved by technology
Method used
Image
Examples
Embodiment 1
[0034] Step 1): Mechanical pretreatment of rice bran. The rice bran was mechanically pulverized by a high-energy nano-impact mill, the temperature of the working chamber was 10°C, and the pulverization time was 0.5 h to obtain 50-mesh rice bran powder.
[0035] Step 2): Composite enzymatic hydrolysis of rice bran powder. The concentration of rice bran substrate is 20 g / L, gelatinization at 100°C for 30min; add liquefying enzyme (5 U / g), react at 85°C for 1h; cool to 40°C after the reaction, add cellulose to the hydrolyzate Enzyme (10 FPU / g), glucoamylase (100 U / g), 50°C, pH 5, enzymatic hydrolysis for 12 h, after enzymatic hydrolysis, the rice bran hydrolyzate was obtained by suction filtration.
[0036] Step 3): Controlled fermentation of rice bran hydrolyzate. Using rice bran hydrolyzate as raw material, fermentation media containing 1%, 2%, 3%, 4% and 5% glucose were prepared, respectively, containing 1 g / L yeast powder, 1 g / L peptone, and 2 mL / L absolute ethanol. L; Ino...
Embodiment 2
[0041] Step 1): Mechanical pretreatment of rice bran. The rice bran was mechanically pulverized by a high-energy nano-impact mill, the temperature of the working chamber was 25 °C, and the pulverization time was 2 h to obtain 100-mesh rice bran powder.
[0042]Step 2): Composite enzymatic hydrolysis of rice bran powder. The concentration of rice bran substrate was 30 g / L, gelatinized at 100°C for 40 minutes; liquefied enzyme (8 U / g) was added, and reacted at 90°C for 2 hours; after the reaction was completed, it was cooled to 50°C, and cellulose was added to the hydrolyzate Enzyme (15 FPU / g), glucoamylase (200 U / g), 50°C, pH 5, enzymatic hydrolysis for 12 h, after enzymatic hydrolysis, the rice bran hydrolyzate was obtained by suction filtration.
[0043] Step 3): Controlled fermentation of rice bran hydrolyzate. Using rice bran hydrolyzate as raw material, fermentation media containing 4% glucose, 2 g / L yeast powder, 3 g / L peptone, and 3 mL / L absolute ethanol were prepared ...
Embodiment 3
[0048] Step 1): Mechanical pretreatment of rice bran. The rice bran was mechanically pulverized by a high-energy nano-impact mill, the temperature of the working chamber was 10°C, and the pulverization time was 0.5 h to obtain 50-mesh rice bran powder.
[0049] Step 2): Composite enzymatic hydrolysis of rice bran powder. The concentration of rice bran substrate is 30 g / L, gelatinization at 100°C for 60min; add liquefying enzyme (10 U / g), react at 85°C for 1h; cool to 60°C after the reaction, add cellulose to the hydrolyzate Enzyme (20 FPU / g), glucoamylase (300 U / g), 50°C, pH 5, enzymatic hydrolysis for 24 h, after enzymatic hydrolysis, the rice bran hydrolyzate was obtained by suction filtration.
[0050] Step 3): Controlled fermentation of rice bran hydrolyzate. Using rice bran hydrolyzate as raw material, fermentation media containing 4% glucose, 5 g / L yeast powder, 5 g / L peptone, and 4 mL / L absolute ethanol were prepared respectively; 2% to 10% of different inoculum volum...
PUM
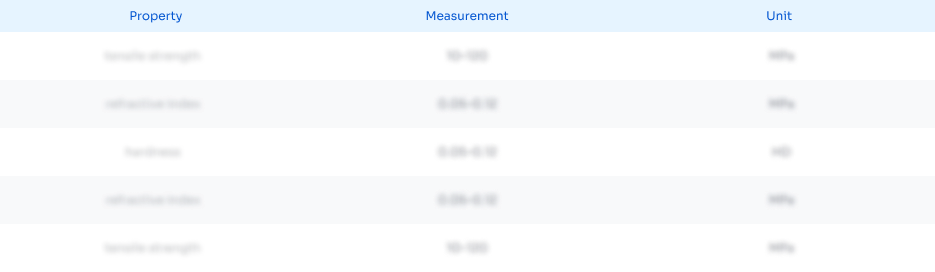
Abstract
Description
Claims
Application Information

- R&D Engineer
- R&D Manager
- IP Professional
- Industry Leading Data Capabilities
- Powerful AI technology
- Patent DNA Extraction
Browse by: Latest US Patents, China's latest patents, Technical Efficacy Thesaurus, Application Domain, Technology Topic, Popular Technical Reports.
© 2024 PatSnap. All rights reserved.Legal|Privacy policy|Modern Slavery Act Transparency Statement|Sitemap|About US| Contact US: help@patsnap.com