Comprehensive recovery method for zinc hydrometallurgy net liquid slag
A technology of hydrometallurgical zinc smelting and recovery method, applied in the field of zinc smelting, can solve the problems of high cost of cobalt removal, electrolytic sintering, poor electrolysis of zinc smelting system, etc.
- Summary
- Abstract
- Description
- Claims
- Application Information
AI Technical Summary
Problems solved by technology
Method used
Image
Examples
Embodiment 1
[0021] Embodiment 1: as figure 1 Shown, a kind of comprehensive recovery method of hydrometallurgy zinc liquid slag, it comprises the following steps successively:
[0022] S1. Low-acid leaching: add net liquid slag, sulfuric acid, and electrolytic waste liquid to the low-acid leaching tank to leaching the net liquid slag, and separate the solid and liquid to obtain copper-enriched slag and net liquid slag leaching solution. The copper-enriched slag is oxidized and Leaching and recovery of metallic copper;
[0023] S2. Iron and arsenic removal: Pour the net liquid slag leaching solution into the iron and arsenic removal neutralization tank, add sodium nitrite for neutralization reaction to remove iron and arsenic, and separate solid and liquid to obtain iron and arsenic waste slag and iron and arsenic removal leaching solution;
[0024] S3. Recovering cobalt: Pour the leaching solution for removing iron and arsenic into the cobalt recovery reaction tank, raise the temperatur...
Embodiment 2
[0026]Embodiment 2: other processing steps and process parameter are identical with embodiment 1; Difference is:
[0027] S3. Recovering cobalt: Pour the leaching solution for removing iron and arsenic into the cobalt recovery reaction tank, raise the temperature to 92°C, add sodium carbonate to adjust the pH value to 4.5, add sodium persulfate for chemical reaction, press S 2 o 3 2+ The molar mass of Fe is 2+ , Mn 2+ , and Co 2+ Sodium persulfate is added at a ratio of 4 times the sum of the moles, and the reaction time is 2 hours. The solid-liquid separation obtains the cobalt slag and the cobalt removal leaching solution; Cobalt slag washing solution, the cobalt slag washing solution returns to the low-acid leaching tank. In this embodiment, the content of cobalt in the leaching solution for removing iron and arsenic is 0.86 g / L, and the content of cobalt in the leaching solution for removing cobalt is 0.016 g / L.
[0028] Embodiment 2: other processing steps and proce...
PUM
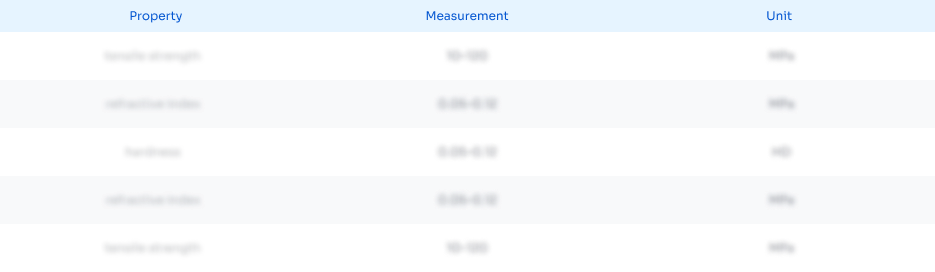
Abstract
Description
Claims
Application Information

- R&D
- Intellectual Property
- Life Sciences
- Materials
- Tech Scout
- Unparalleled Data Quality
- Higher Quality Content
- 60% Fewer Hallucinations
Browse by: Latest US Patents, China's latest patents, Technical Efficacy Thesaurus, Application Domain, Technology Topic, Popular Technical Reports.
© 2025 PatSnap. All rights reserved.Legal|Privacy policy|Modern Slavery Act Transparency Statement|Sitemap|About US| Contact US: help@patsnap.com