Arsenic alkali slag resource utilization device and method thereof
A technology for recycling arsenic-alkali slag, which is applied in the field of resource utilization equipment for arsenic-alkali slag. The effect of power consumption
- Summary
- Abstract
- Description
- Claims
- Application Information
AI Technical Summary
Problems solved by technology
Method used
Image
Examples
Embodiment 1
[0057] as attached figure 1 As shown, the device for resource utilization of arsenic-alkali slag in this embodiment mainly includes: electric heating reduction furnace (1), powder lock air meter feeding device (2), ammonia injection device (3), cooling (heat exchange) device (4), residual ammonia finishing device (5), centrifugal fan (6), ammonia storage device (7), the discharge port of the powder lock air meter feeding device (2) and the electrothermal reduction furnace (1 ), the ammonia injection device (3) is connected with the electrothermal reduction furnace (1), the cooling (heat exchanger) (4) with the ammonia gas delivery pipeline, and the cooling (heat exchanger) (4) is respectively connected with the electric heating The exhaust outlet of the reduction furnace (1) and the inlet of the residual ammonia finishing device (5) are connected by pipes, the waste gas outlet of the residual ammonia finishing device (5) is connected with the air inlet of the centrifugal fan (...
Embodiment 2
[0066]as attached figure 2 As shown, the device for resource utilization of arsenic-alkali slag in this embodiment mainly includes: electric heating reduction furnace (1), powder lock air meter feeding device (2), ammonia injection device (3), cooling (heat exchange) device (4), residual ammonia finishing device (5), centrifugal fan (6), ammonia storage device (7), the discharge port of the powder lock air meter feeding device (2) and the electrothermal reduction furnace (1 ), the ammonia injection device (3) is connected with the electrothermal reduction furnace (1) and the cooling (heat exchanger) (4) respectively with the ammonia gas delivery pipeline, and the inlet of the cooling (heat exchanger) (4) is connected with The exhaust outlet of the electrothermal reduction furnace (1) is connected, the centrifugal fan (6) is connected with the exhaust gas outlet of the cooling (heat exchanger) (4) and the inlet of the residual ammonia finishing device (5) by pipelines, and the...
Embodiment 3
[0074] The device for recycling the arsenic-alkali slag in this embodiment is the same as that in Embodiment 1.
[0075] The arsenic-alkali slag produced by an antimony smelter was selected as the raw material, and the chemical composition (average value) of the raw material was: As: 22.92%,
[0076] Sb: 34.85%, Pb 3.27%, Na: 27.78%, arsenic-alkali slag plus 15% by mass of rice husk pre-grinded into a 160-mesh sieve with 5% of the remaining powder; commercially available liquid ammonia was selected as the reducing agent; in the test Device line test.
[0077] The method for resource utilization of arsenic-alkali slag in this embodiment includes the following steps: liquid ammonia is vaporized by a heat exchange device and the temperature is raised to 250°C. The arsenic-alkali slag powder material preheated to 350°C±10°C is continuously fed into the electrothermal reduction furnace at 800°C±10°C, and the bottom spray method is used to directly inject ammonia into the material ...
PUM
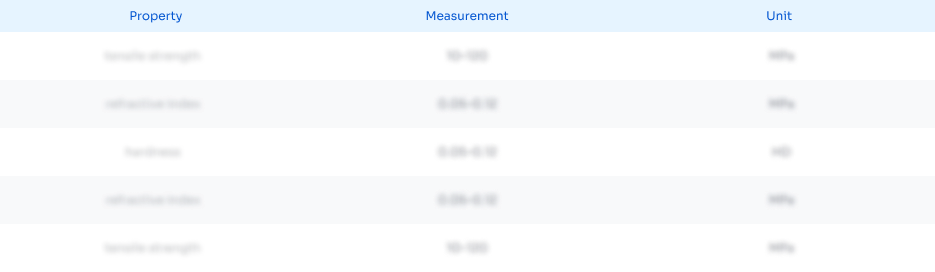
Abstract
Description
Claims
Application Information

- R&D
- Intellectual Property
- Life Sciences
- Materials
- Tech Scout
- Unparalleled Data Quality
- Higher Quality Content
- 60% Fewer Hallucinations
Browse by: Latest US Patents, China's latest patents, Technical Efficacy Thesaurus, Application Domain, Technology Topic, Popular Technical Reports.
© 2025 PatSnap. All rights reserved.Legal|Privacy policy|Modern Slavery Act Transparency Statement|Sitemap|About US| Contact US: help@patsnap.com