Sheet heating multifunctional and small infrared composite box type heating furnace and method
A heating furnace and box-type technology, applied in the field of hot stamping, can solve the problems of high construction cost, unsuitable heating speed, large floor area, etc., to ensure temperature uniformity, shorten heating time, and shorten floor space Effect
- Summary
- Abstract
- Description
- Claims
- Application Information
AI Technical Summary
Problems solved by technology
Method used
Image
Examples
example 1
[0073] The present invention adopts the infrared heating furnace of the upper-mounted infrared composite box-type heating furnace to heat ordinary low-carbon steel. Figure 9 280mm×200mm×2mm multi-gradient I-shaped ultra-low carbon steel plate ( Figure 9 ) at 288kw / m 2The output power, the temperature change when the heating height is 4.5cm, and the distance between the infrared lamps is 2mm. Such as Figure 10 shown. The steel plates are mutually symmetrical, and 1 / 4 of the steel plate is selected as the measurement range. (Position iv point is the temperature measurement of the center of the I-shaped plate (point 4), position i point is the 50×50 inflection point temperature of the I-shaped plate (point 1), and position iii point is the edge temperature of the I-shaped plate (point 3) ).
example 2
[0075] The infrared heating furnace of the top-mounted infrared composite box-type heating furnace is also used to heat ordinary low-carbon steel, the heating distance is still 4.5cm, and the output power of the short-wave infrared lamp is adjusted to 360kw / m 2 , the thickness and shape of the steel plate remain unchanged, and the temperature changes in four places are measured. (Position iv point is the center temperature measurement curve of the I-shaped plate (point 4), position iii point is the edge temperature (point 3), position i point is the inflection point temperature of 50×50 (point 1), position ii point is 50×25 The inflection point temperature (point 2)). Such as Figure 11 shown.
example 3
[0077] The infrared heating furnace of the upper-mounted infrared composite box-type heating furnace is used to heat ordinary low-carbon steel. The thickness of the low-carbon steel of the same material becomes 1mm, the heating height is adjusted to 7cm, and the distance between the lamp tubes is adjusted to 1.5mm. , at this time the output power of the short-wave infrared lamp is 288kw / m 2 , use the same single-layer infrared heating furnace to heat the steel plate, the shape of the steel plate remains unchanged, and measure the temperature changes at four places. (The position iv point is the temperature measurement curve (point 4) of the center point, the position ii point is the inflection point temperature (point 2) of 50×25 of the I-shaped plate, and the position v point is the temperature of the center point of the back side of the I-shaped plate ( point 5), the position i point is the inflection point temperature of 50×50 (point 1)). Such as Figure 12 shown.
PUM
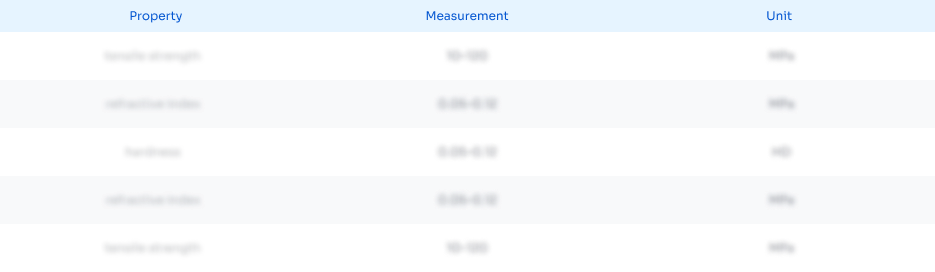
Abstract
Description
Claims
Application Information

- R&D Engineer
- R&D Manager
- IP Professional
- Industry Leading Data Capabilities
- Powerful AI technology
- Patent DNA Extraction
Browse by: Latest US Patents, China's latest patents, Technical Efficacy Thesaurus, Application Domain, Technology Topic, Popular Technical Reports.
© 2024 PatSnap. All rights reserved.Legal|Privacy policy|Modern Slavery Act Transparency Statement|Sitemap|About US| Contact US: help@patsnap.com