Structural material and preparation method thereof, 3D printing product
A technology for constructing materials and raw materials, which is applied in the field of 3D printing materials and can solve problems such as poor performance
- Summary
- Abstract
- Description
- Claims
- Application Information
AI Technical Summary
Problems solved by technology
Method used
Image
Examples
preparation example Construction
[0049] See figure 1 , an embodiment of the present invention also provides a method for preparing a construction material, comprising the following steps:
[0050] S10. According to the parts by mass, 50-70 parts of synthetic wax, 10-20 parts of microcrystalline wax and 2-10 parts of montan ester wax are mixed and melted. Wherein, the synthetic wax is selected from at least one of SX55R synthetic wax, SX60S synthetic wax and SX70 synthetic wax, and the microcrystalline wax is selected from DNW-160S microcrystalline wax, DNW-170S microcrystalline wax, S682 microcrystalline wax and W445 microcrystalline wax At least one of the waxes, the montan ester wax is selected from at least one of E wax, OP wax and LP wax.
[0051] S20, followed by 5-20 parts of tackifier, 2-10 parts of toughening agent, 0.5-2 parts of plasticizer, 0.1-0.5 parts of phase change crystal form inducer and 0.1- Mix 0.5 parts of the phase change accelerator at 100°C to 110°C, filter and keep the filtrate to o...
Embodiment 1
[0055] Add 70.0g of SX60S synthetic wax, 15.3g of W445 microcrystalline wax and 2.0g of LP wax into the reaction kettle, adjust the temperature to 100°C, and uniformly melt to obtain the basic wax liquid A.
[0056] 5.2g C5 hydrogenated petroleum resin, 1.6g polycaprolactone, 4.0g ethylene propylene copolymer with a molecular weight of 300-1000, 1.0g epoxy soybean oil, 0.2g dehydroabietic acid alkali metal salt, 0.3g polypara Ethylene glycol phthalate, 0.1g styrene-ethylene-butylene-styrene block copolymer and 0.3g butyl hydroxyanisole were sequentially added to the base wax solution A, the temperature was controlled at 110°C, and the temperature was controlled at 700r / The stirring speed of min was stirred for 1 h to obtain wax liquid B.
[0057] Filter the wax liquid B through a suction filter bottle with a 1 μm filter element while it is hot, and bottle the filtrate to obtain the construction material.
Embodiment 2
[0059] Add 50.0g of SX55R synthetic wax, 18.3g of DNW-170S microcrystalline wax and 7.9g of E wax into the reaction kettle, adjust the temperature to 110°C, and uniformly melt to obtain the basic wax liquid A.
[0060] 18.1g terpene phenolic resin, 2.0g poly-α-methylstyrene resin, 2.0g white mineral oil, 0.1g bis(3,4-dimethylbenzylidene) sorbitol, 0.5g sodium benzoate, 1.0 Add 1 g of maleic anhydride-grafted polypropylene wax and 0.1 g of tert-butylhydroquinone to base wax liquid A, control the temperature at 110° C., and stir at a stirring speed of 500 r / min for 2 h to obtain wax liquid B.
[0061] Filter the wax liquid B through a suction filter bottle with a 1 μm filter element while it is hot, and bottle the filtrate to obtain the construction material.
PUM
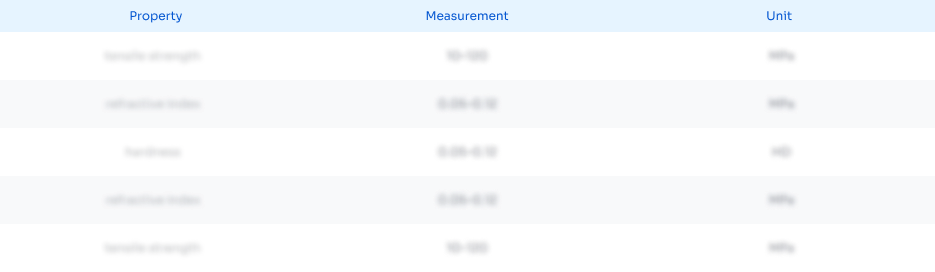
Abstract
Description
Claims
Application Information

- R&D
- Intellectual Property
- Life Sciences
- Materials
- Tech Scout
- Unparalleled Data Quality
- Higher Quality Content
- 60% Fewer Hallucinations
Browse by: Latest US Patents, China's latest patents, Technical Efficacy Thesaurus, Application Domain, Technology Topic, Popular Technical Reports.
© 2025 PatSnap. All rights reserved.Legal|Privacy policy|Modern Slavery Act Transparency Statement|Sitemap|About US| Contact US: help@patsnap.com