Resin matrix with strong microwave absorbability and preparation method thereof
A technology of microwave absorption and resin matrix, applied in the field of composite materials, can solve the problems of poor microwave absorption capacity of resin matrix, large temperature fluctuation of resin system, poor compatibility of resin matrix, etc., and achieves good microwave absorption performance, optimized curing temperature and Curing, curing uniform effect
- Summary
- Abstract
- Description
- Claims
- Application Information
AI Technical Summary
Problems solved by technology
Method used
Image
Examples
Embodiment 1
[0022] The main resin is 1,4-bis(hydroxyhexafluoroisopropyl)benzene diglycidyl ether, the microwave absorption component is ethylene glycol diglycidyl ether modified imidazole ionic liquid, and the ionic liquid modified nanometer component is microwave absorption Component Modified SiO 2 Microspheres, the curing agent uses 1,3-bis-(γ-aminopropyl)-5,5-dimethylhydantoin and bis(3-aminophenyl)methylphosphine oxide (BAMPO) according to the mass fraction of 10 :10 compound, the carbon fiber is T700 from Toray Corporation of Japan. The mass ratio of the main resin, the microwave absorbing component, the curing agent and the ionic liquid modified nano component is 100:4:20:0.1. The preparation process is as follows: 1-butyl-3 methylimidazolium tetrafluoroborate and ethylene glycol diglycidyl ether are mixed according to the ratio of parts by mass of 100:70. The mixing conditions are nitrogen atmosphere, oil bath temperature 45°C, The stirring speed is 800 rpm, and the time is 10 mi...
Embodiment 2
[0027] The main resin adopts dibromopentaerythiol diglycidyl ether, the microwave absorbing component adopts 1,2-propanediol diglycidyl ether modified imidazole ionic liquid, and the ionic liquid modified nanometer component adopts microwave absorbing component to modify carbon nanometer tube, the curing agent is 1,3-bis-(γ-aminopropyl)-5,5-dimethylhydantoin and 4-(4-hydroxyphenyl)-2,3-naphthyridine-1- The ketone is a compound with a mass fraction of 20:25, and the carbon fiber is T700 from Toray Corporation of Japan. The mass ratio of the main resin, the microwave absorbing component, the curing agent and the ionic liquid modified nano component is 100:5:45:0.5. The preparation process is as follows: 1-butyl-3-methylimidazolium tetrafluoroborate and 1,2-propanediol diglycidyl ether are mixed according to the ratio of parts by mass of 100:90, the mixing conditions are nitrogen atmosphere, oil bath temperature 50 ℃, stirring speed 700 rpm, time 5min. Then react in a nitrogen ...
Embodiment 3
[0032] The main resin adopts dibromopentaerythiol diglycidyl and 2,3-bis(2,3-epoxypropylthioethylthio)propyl 2,3-epoxypropylsulfide epoxy resin according to The compound with a mass fraction of 50:50, the microwave absorbing component uses ethylene glycol diglycidyl ether and neopentyl glycol diglycidyl ether to modify the imidazole ionic liquid according to the compound with a mass fraction of 4:1, the ion The liquid modified nano-component uses microwave absorbing components to modify graphene and Fe with a mass fraction of 0.4:0.2 3 o 4 Nanoparticle mixture, 4-(4-hydroxyphenyl)-2,3-naphthyridine-1-one as curing agent, and T700 from Toray Corporation of Japan as carbon fiber. The mass ratio of the main resin, the microwave absorbing component, the curing agent and the ionic liquid modified nano component is 100:5:30:0.6. The preparation process is as follows: mix 1-butyl-3 methylimidazolium tetrafluoroborate, ethylene glycol diglycidyl ether and neopentyl glycol diglycidyl...
PUM
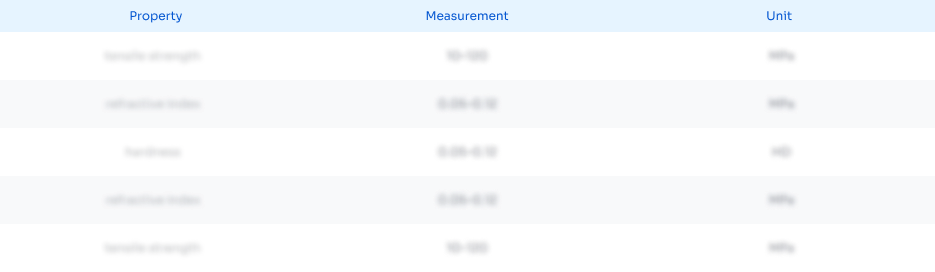
Abstract
Description
Claims
Application Information

- R&D Engineer
- R&D Manager
- IP Professional
- Industry Leading Data Capabilities
- Powerful AI technology
- Patent DNA Extraction
Browse by: Latest US Patents, China's latest patents, Technical Efficacy Thesaurus, Application Domain, Technology Topic, Popular Technical Reports.
© 2024 PatSnap. All rights reserved.Legal|Privacy policy|Modern Slavery Act Transparency Statement|Sitemap|About US| Contact US: help@patsnap.com