Novel hydrolysis resistant polyurethane composite material, preparation method and application thereof in hydrolysis resistant cable products
A composite material and polyether polyurethane technology, which is applied in the direction of plastic/resin/wax insulators, organic insulators, electrical components, etc., can solve the problems of restricting the development and application of polyurethane, high control cost of modification process, and restricting development and application. Good anti-hydrolysis function, excellent anti-hydrolysis function, and good application prospects
- Summary
- Abstract
- Description
- Claims
- Application Information
AI Technical Summary
Problems solved by technology
Method used
Examples
Embodiment 1
[0031] Under the environment of heating and heating, add 15 parts by weight of formaldehyde mixed with 10 parts by weight of epoxy silane to the uniformly mixed mixture of 100 parts by weight of polyether polyurethane elastomer and 10 parts by weight of phenol and mix evenly. While reacting at a constant temperature at ℃, add 3.6 parts by weight of triphenyl phosphate, 1 part by weight of zinc borate, 0.4 parts by weight of barium hydroxide, 1.5 parts by weight of triethylpropyl phosphite, and 0.5 parts by weight of dialkyl dithiophosphoric acid Molybdenum, 0.7 parts by weight of carbon black, 0.2 parts by weight of glass fiber, 0.1 part by weight of talc, and 1 part by weight of lead dibasic phosphite are uniformly mixed. After the reaction is completed, the material is discharged and cooled to obtain a polyurethane composite material.
[0032] The waterproof and waterproof cable products prepared by the polyurethane composite material in this implementation were hydrolyzed at...
Embodiment 2
[0034] Under the environment of heating and heating, add 33 parts by weight of formaldehyde mixed with 15 parts by weight of aminosilane to the uniformly mixed mixture of 100 parts by weight of polyether polyurethane elastomer and 22 parts by weight of hydroquinone and mix evenly. While reacting at a constant temperature of 110°C, add 5 parts by weight of tris(2,3-dichloropropyl) phosphate, 2 parts by weight of barium metaborate, 1 part by weight of magnesium hydroxide, and 2.5 parts by weight of triisodecyl phosphite , 1.5 parts by weight of zinc dialkyldithiophosphate, 2.8 parts by weight of carbon black, 1.4 parts by weight of glass fiber, 0.8 parts by weight of calcium silicate, 3 parts by weight of aluminum stearate, and mix uniformly. After the reaction finishes, discharging After cooling, the polyurethane composite material is obtained.
[0035]The waterproof and waterproof cable products prepared by the polyurethane composite material in this implementation were hydrol...
Embodiment 3
[0037] Under the heating and heating environment, add 42 parts by weight of formaldehyde mixed with 20 parts by weight of aminosilane to the uniformly mixed mixture of 100 parts by weight of polyether polyurethane elastomer and 28 parts by weight of p-hydroxymethylphenol and mix evenly. While reacting at a constant temperature of -106°C, add 6.3 parts by weight of triphenyl phosphate, 2.5 parts by weight of calcium metaborate, 1.2 parts by weight of barium sulfate, 3.6 parts by weight of triethylpropyl phosphite, and 1.4 parts by weight of dialkyl disulfide Antimony phosphate, 4.5 parts by weight of carbon black, 2.5 parts by weight of glass fiber, 1 part by weight of talc, and 5 parts by weight of dibasic lead stearate are mixed uniformly. After the reaction is completed, the material is cooled to obtain a polyurethane composite material.
[0038] The waterproof cable products prepared from the polyurethane composite material in this implementation were hydrolyzed at 70°C and ...
PUM
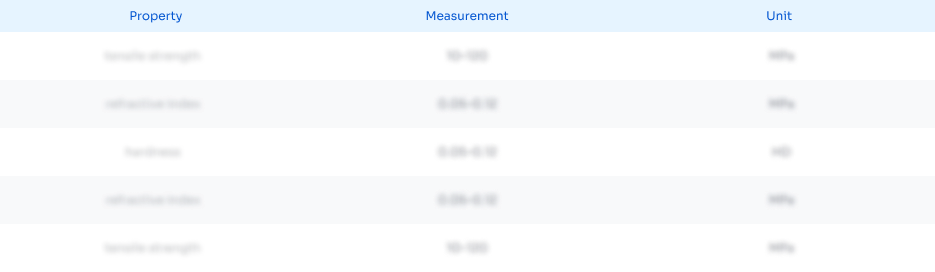
Abstract
Description
Claims
Application Information

- R&D
- Intellectual Property
- Life Sciences
- Materials
- Tech Scout
- Unparalleled Data Quality
- Higher Quality Content
- 60% Fewer Hallucinations
Browse by: Latest US Patents, China's latest patents, Technical Efficacy Thesaurus, Application Domain, Technology Topic, Popular Technical Reports.
© 2025 PatSnap. All rights reserved.Legal|Privacy policy|Modern Slavery Act Transparency Statement|Sitemap|About US| Contact US: help@patsnap.com