A method for preparing YAG transparent ceramics by adopting core-shell structure powder
A core-shell structure and transparent ceramic technology is applied in the field of preparing YAG transparent ceramics by using core-shell structure powder, which can solve the problems of insufficiently satisfying industrial production needs, low yield of YAG raw material powder, and large precursor particle size. Achieve the effect of realizing technology promotion and commercial promotion, short preparation cycle, simple and easy operation of preparation process
- Summary
- Abstract
- Description
- Claims
- Application Information
AI Technical Summary
Problems solved by technology
Method used
Image
Examples
Embodiment 1
[0036] (1) Add 0.5mol / L of Y(NO 3 ) 3 The solution was added to the Al at a rate of 0.5ml / min 2 o 3 In the suspension, the precipitating agent is urea, the amount of ions added satisfies the stoichiometric ratio of Y:Al=3:5, and the reaction temperature is 50°C;
[0037] (2) the urea used in step (1) is added to Al as a pH regulator 2 o 3 In the slurry, keep the slurry pH=8.8, and the solid content is 35vol.%.
[0038] (3) directly filtering the slurry obtained in step (2), without washing, the core-shell structure powder can be obtained;
[0039] (4) Dry the powder obtained in step (3) in a constant temperature oven at 100°C for 24 hours, and calcinate the obtained powder at a low temperature of 300°C for 1 hour;
[0040] (5) Add sintering aid silicon dioxide and ammonium bicarbonate solution with pH=9 to the calcined powder, mix by ball milling for 10 hours, the rotating speed of ball milling is 165r / min; Dry in an oven for 12 hours, and pass the resulting powder thro...
Embodiment 2
[0045] (1) Add 0.8mol / L of Y(NO 3 ) 3 The solution was added to the Al at a rate of 3ml / min 2 o 3 In the suspension, the precipitant is urea, the amount of ions added satisfies the stoichiometric ratio of Y:Al=3:5, and the reaction temperature is 80°C;
[0046] (2) the urea used in step (1) is added to Al as a pH regulator 2 o 3 In the slurry, keep the slurry pH=9.1, and the solid content is 60vol.%.
[0047] (3) directly filtering the slurry obtained in step (2), without washing, the core-shell structure powder can be obtained;
[0048] (4) drying the powder obtained in step (3) in a constant temperature oven at 120°C for 24 hours, and calcining the obtained powder at a low temperature of 500°C for 2 hours;
[0049] (5) Add sintering aid magnesia and ammonium carbonate solution with pH=8 to the calcined powder, mix by ball milling for 16 hours, the rotating speed of ball milling is 155r / min; put the obtained slurry in a constant temperature oven at 75°C After drying fo...
Embodiment 3
[0054] (1) Add 0.6mol / L of Y(NO 3 ) 3 The solution was added to the Al at a rate of 2ml / min 2 o 3 In the suspension, the precipitating agent is urea, the amount of ions added satisfies the stoichiometric ratio of Y:Al=3:5, and the reaction temperature is 65°C;
[0055] (2) the urea used in step (1) is added to Al as a pH regulator 2 o 3 In the slurry, keep the slurry pH=9, and the solid content is 50vol.%;
[0056] (3) directly filtering the slurry obtained in step (2), without washing, the core-shell structure powder can be obtained;
[0057] (4) Dry the powder obtained in step (3) in a constant temperature oven at 110°C for 18 hours, and calcinate the obtained powder at a low temperature of 400°C for 1.5 hours;
[0058] (5) Add sintering aid calcium oxide and urea solution with pH = 7.2 to the calcined powder, mix by ball milling for 16 hours, the speed of ball milling is 155r / min; dry the obtained slurry in a constant temperature oven at 65°C 18h, the gained powder i...
PUM
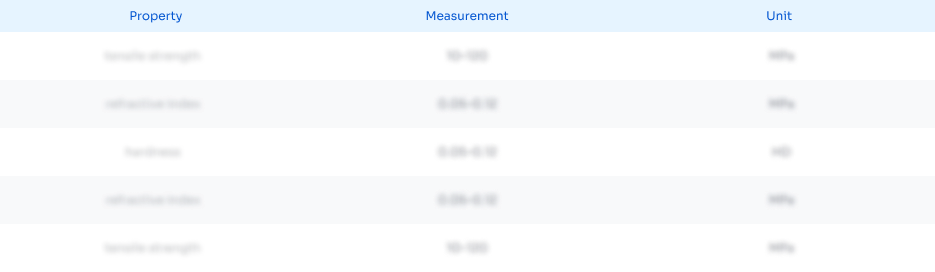
Abstract
Description
Claims
Application Information

- Generate Ideas
- Intellectual Property
- Life Sciences
- Materials
- Tech Scout
- Unparalleled Data Quality
- Higher Quality Content
- 60% Fewer Hallucinations
Browse by: Latest US Patents, China's latest patents, Technical Efficacy Thesaurus, Application Domain, Technology Topic, Popular Technical Reports.
© 2025 PatSnap. All rights reserved.Legal|Privacy policy|Modern Slavery Act Transparency Statement|Sitemap|About US| Contact US: help@patsnap.com