A kind of preparation method of fesi alloy powder with high direct current superposition characteristic
A high DC superposition, alloy powder technology, applied in metal processing equipment, transportation and packaging, etc., can solve problems such as poor superposition characteristics, and achieve the effect of reducing the complexity of smelting operations, uniform composition, and good formability
- Summary
- Abstract
- Description
- Claims
- Application Information
AI Technical Summary
Problems solved by technology
Method used
Image
Examples
Embodiment 1
[0037]A method for preparing FeSi alloy powder with high DC superposition characteristics in this embodiment specifically includes the following steps:
[0038] A) Batching Each raw material is weighed and batched, and the weight percentage of each raw material is: silicon 3.75%, manganese 0.03%, chromium 0.02%, iron is a surplus, and raw materials include rod-shaped polished iron and massive metal silicon;
[0039] B) Melting Put the prepared charge into the melting furnace, adopt the non-vacuum melting process, set the power of the intermediate frequency furnace, gradually increase from 0kw to the normal smelting power to 500kw, first melt the iron, and reduce the power of the intermediate frequency furnace to 0kw after the iron is melted Pick up the iron slag, then increase the power of the intermediate frequency furnace to 500kw to melt silicon, reduce the power of the intermediate frequency furnace to 0kw after the silicon is melted, remove the slag on the surface of the a...
Embodiment 2
[0068] A method for preparing FeSi alloy powder with high DC superposition characteristics in this embodiment specifically includes the following steps:
[0069] A) batching Each raw material is carried out weighing batching, and each raw material percentage by weight is: silicon 4.5%, manganese 0.04%, chromium 0.02%, iron is surplus;
[0070] B) Smelting Put the prepared charge into the smelting furnace, adopt the non-vacuum smelting process, set the power of the intermediate frequency furnace, gradually increase from 0kw to the normal smelting power to first melt 450kw iron, and reduce the power of the intermediate frequency furnace to 25kw after the iron is melted Pick up the iron slag, then increase the power of the intermediate frequency furnace to 500kw to melt silicon, reduce the power of the intermediate frequency furnace to 25kw after the silicon is melted, remove the slag on the surface of the alloy melt, and then keep the power of 250kw for refining, after refining f...
PUM
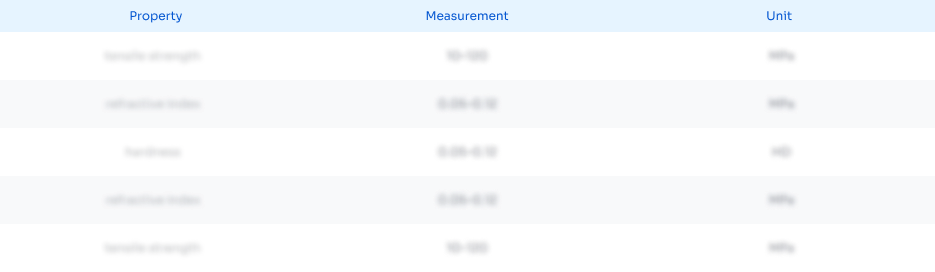
Abstract
Description
Claims
Application Information

- Generate Ideas
- Intellectual Property
- Life Sciences
- Materials
- Tech Scout
- Unparalleled Data Quality
- Higher Quality Content
- 60% Fewer Hallucinations
Browse by: Latest US Patents, China's latest patents, Technical Efficacy Thesaurus, Application Domain, Technology Topic, Popular Technical Reports.
© 2025 PatSnap. All rights reserved.Legal|Privacy policy|Modern Slavery Act Transparency Statement|Sitemap|About US| Contact US: help@patsnap.com