Process method for granulating or coating graphite negative electrode material
A graphite negative electrode and process method technology, applied in graphite, chemical instruments and methods, battery electrodes, etc., can solve the problems of unfavorable product post-processing, low product vibration, wide particle size distribution, etc., to improve processing performance and use performance , improve the cycle life and charging rate, and the effect of narrow particle size distribution
- Summary
- Abstract
- Description
- Claims
- Application Information
AI Technical Summary
Problems solved by technology
Method used
Image
Examples
Embodiment 1
[0039] Put the artificial graphite powder material with a particle size of 9 μm into the reactor, then keep stirring at a speed of 15 rpm, and rapidly raise the temperature to T1 and keep the temperature constant for 4 hours, T1=150°C;
[0040] At a constant temperature of 150°C, the solution binder formed by solid powder pitch-quinoline is sprayed onto the surface of the material in the reactor. The ratio of carbon source powder material to solid powder pitch is 100:9. The process is kept stirring to form an overall uniform materials;
[0041] At a stirring speed of 45rmp, raise the temperature from 150°C to 600°C at a speed of 5°C / min and keep the temperature constant for 2 hours, then raise the temperature to T2 at 2°C / min and keep the temperature constant for 3 hours to form stable composite particles, T2=850°C;
[0042] Cool to less than 50°C and discharge, then enter the roller kiln for carbonization at 1300°C;
[0043] After the carbonization is completed, mix, sieve, ...
Embodiment 2
[0045] Put the artificial graphite powder material with a particle size of 14 μm into the reaction kettle, then keep stirring at a speed of 25 rpm, and quickly raise the temperature to T1 and keep the temperature constant for 1 hour, T1=30°C;
[0046] At a constant temperature of 30°C, the petroleum liquid asphalt binder is sprayed onto the surface of the material in the reactor. The ratio of the carbon source powder material to the petroleum liquid asphalt is 100:25, and the process is kept stirring to form an overall uniform material;
[0047] At a stirring speed of 30rmp, raise the temperature from 150°C to 500°C at a speed of 3°C / min and keep the temperature constant for 3 hours, then raise the temperature to T2 at a rate of 2°C / min and keep the temperature constant for 4 hours to form stable composite particles, T2=650°C;
[0048] Cool to less than 50°C and discharge, then enter the roller kiln for carbonization at 1100°C;
[0049] After the carbonization is completed, mi...
Embodiment 3
[0051] Put the artificial graphite powder material with a particle size of 6 μm into the reaction kettle, then keep stirring at a speed of 18rmp, and quickly raise the temperature to T1 and keep the temperature constant for 2 hours, T1=280°C;
[0052] Spray the solution coating agent formed by solid powder polyvinylidene fluoride and N,N-dimethylformamide at a constant temperature of 180°C to the surface of the material in the reactor. The ratio of artificial graphite powder material to solid powder polyvinylidene fluoride is 100:6, the process is kept stirring to form an overall uniform material;
[0053]At a stirring speed of 25rmp, raise from 150°C to T2 at a speed of 3°C / min and keep the temperature constant for 2 hours, the coating agent forms a stable coating layer on the surface of the material, T2=600°C;
[0054] Cool to less than 50°C and discharge, then enter the roller kiln for carbonization at 900°C;
[0055] After the carbonization is completed, mix, sieve, and d...
PUM
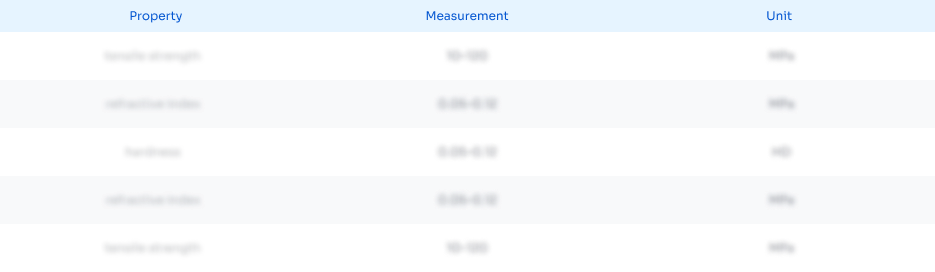
Abstract
Description
Claims
Application Information

- Generate Ideas
- Intellectual Property
- Life Sciences
- Materials
- Tech Scout
- Unparalleled Data Quality
- Higher Quality Content
- 60% Fewer Hallucinations
Browse by: Latest US Patents, China's latest patents, Technical Efficacy Thesaurus, Application Domain, Technology Topic, Popular Technical Reports.
© 2025 PatSnap. All rights reserved.Legal|Privacy policy|Modern Slavery Act Transparency Statement|Sitemap|About US| Contact US: help@patsnap.com