Preparation method of electrostatic fiber and product thereof
An electrostatic fiber and electrostatic technology, applied in the field of electrostatic fiber preparation method and the resulting products, can solve the problems of non-recyclable, waste of water resources, difficulty in continuous production, etc., to enhance electrostatic adsorption capacity, reduce hair and broken head, producing continuous and stable effects
- Summary
- Abstract
- Description
- Claims
- Application Information
AI Technical Summary
Problems solved by technology
Method used
Image
Examples
preparation example Construction
[0023] Such as figure 1 As shown, the embodiment of the present invention provides a method for preparing an electrostatic fiber, comprising the following steps:
[0024] Add the raw material and electrostatic masterbatch into the extruder to form the primary fiber, and the primary fiber passes through the oil agent roller, the godet roller, the first drafting machine, the second drafting machine, the third drafting machine, the stacking machine, After the crimping machine and the heat setting machine, the fiber bundles are obtained, and the fiber bundles pass through the cutting machine to obtain electrostatic fibers; wherein, the oiling agent on the oiling roller is replaced with water, and between the oiling agent roller and the godet roller, two traction Water spray units are added to the drawing machine, three drafting machines, and the front end of the crimping machine to spray water to the fiber bundles, and a spray unit is added to the tail end of the heat setting mach...
Embodiment 1
[0045] Add polypropylene Z30S raw material and electrostatic masterbatch (addition amount is 5%) into the extruder to form the primary fiber, and the primary fiber passes through the oil agent roller, the godet roller, the first drafting machine, the second drafting machine, Fiber bundles are obtained after the three-pass drafting machine, stacking machine, crimping machine, and heat setting machine, and the fiber bundles pass through a cutting machine to obtain electrostatic fibers; wherein, the oiling agent on the oiling roller is replaced with water, and the oiling agent on the oiling roller Between the fiber bundle and the godet roller, at the second drafting machine, at the third drafting machine, and at the front end of the crimper, add water spray points to spray water to the fiber bundles, and add water spray points at the end of the heat setting machine to Spray water mist on the fiber bundle. The specific parameters of each link are shown in Table 2. In this table, t...
Embodiment 2
[0050] The 2D electrostatic fiber prepared in Example 1 and the 2D oil-containing fiber prepared by the original normal oiling (the difference between the production process of the normal oil-containing fiber and the production process of the electrostatic fiber is that the spinning aid used in the production process is oil agent or water, and other processes are exactly the same) from the four aspects of linear density, breaking strength, elongation at break, and oil content, and the comparison data is shown in Table 3 and Table 4.
[0051] Table 3 Performance data of 2D electrostatic fibers
[0052]
[0053] Table 4 Performance data of 2D oil-containing fibers
[0054]
[0055] From the comparison of the data in Table 3 and Table 4, it can be seen that the oil content of the electrostatic fiber is 0%, that is, there is no oil agent, and the breaking strength and elongation at break of the fiber basically do not change. And because the electrostatic fiber does not cont...
PUM
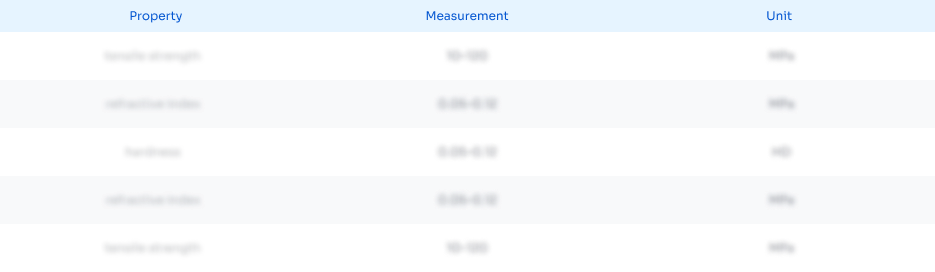
Abstract
Description
Claims
Application Information

- R&D
- Intellectual Property
- Life Sciences
- Materials
- Tech Scout
- Unparalleled Data Quality
- Higher Quality Content
- 60% Fewer Hallucinations
Browse by: Latest US Patents, China's latest patents, Technical Efficacy Thesaurus, Application Domain, Technology Topic, Popular Technical Reports.
© 2025 PatSnap. All rights reserved.Legal|Privacy policy|Modern Slavery Act Transparency Statement|Sitemap|About US| Contact US: help@patsnap.com