Production device and production method of continuous fiber reinforced thermoplastic composite
A technology for enhancing thermoplasticity and continuous fiber, which is applied in the field of composite material production equipment, can solve the problem that continuous fiber is not easy to completely infiltrate, and achieve the effect of enhancing product strength and ensuring product quality
- Summary
- Abstract
- Description
- Claims
- Application Information
AI Technical Summary
Problems solved by technology
Method used
Image
Examples
Embodiment 1
[0034] A production method of continuous fiber reinforced thermoplastic composite material includes the following steps:
[0035] 1) The continuous glass fiber bundle 100 (Owens Corning OC-SE4850-1200Tex) is led out from the creel 1, and then transmitted through the tension spreading device 2 and then introduced into the fiber impregnation structure 5;
[0036] 2) Turn on the supercritical carbon dioxide generator 4 and inject supercritical carbon dioxide into the molten thermoplastic resin. The molten thermoplastic resin is located in the screw barrel 31 of the screw extruder 3 to obtain a carbon dioxide-containing molten thermoplastic resin; wherein the thermoplastic resin is Polycarbonate. The temperature of the screw barrel 31 of the screw extruder 3 is 240°C. In the supercritical carbon dioxide generator 4, the pressure control valve 42 is adjusted so that the pressure of the supercritical carbon dioxide after the pressure control valve 42 is 8.5 MPa, and the positive metering...
Embodiment 2
[0040] A production method of continuous fiber reinforced thermoplastic composite material includes the following steps:
[0041] 1) The continuous glass fiber bundle 100 (Zhejiang Jushi 352A 1200Tex) is led out from the creel 1, and then transferred through the tension spreading device 2 and then introduced into the fiber impregnation structure 5;
[0042] 2) Turn on the supercritical carbon dioxide generator 4 and inject supercritical carbon dioxide into the molten thermoplastic resin. The molten thermoplastic resin is located in the screw barrel 31 of the screw extruder 3 to obtain a carbon dioxide-containing molten thermoplastic resin; wherein the thermoplastic resin is Polyethylene terephthalate (PET). The temperature of the screw barrel 31 of the screw extruder 3 is 280°C. In the supercritical carbon dioxide generator 4, the pressure control valve 42 is adjusted so that the pressure of the supercritical carbon dioxide after the pressure control valve 42 is 10 MPa, and the pos...
Embodiment 3
[0046] A production method of continuous fiber reinforced thermoplastic composite material includes the following steps:
[0047] 1) The continuous glass fiber bundle 100 (Zhejiang Jushi 362A 1200Tex) is drawn from the creel 1 and transferred through the tension spreading device 2 and then introduced into the fiber impregnation structure 5;
[0048] 2) Turn on the supercritical carbon dioxide generator 4 and inject supercritical carbon dioxide into the molten thermoplastic resin. The molten thermoplastic resin is located in the screw barrel 31 of the screw extruder 3 to obtain a carbon dioxide-containing molten thermoplastic resin; wherein the thermoplastic resin is Polylactic acid (PLA). The temperature of the screw barrel 31 of the screw extruder 3 is 200°C. In the supercritical carbon dioxide generator 4, the pressure control valve 42 is adjusted so that the pressure of the supercritical carbon dioxide after the pressure control valve 42 is 8.15 MPa, and the positive metering pu...
PUM
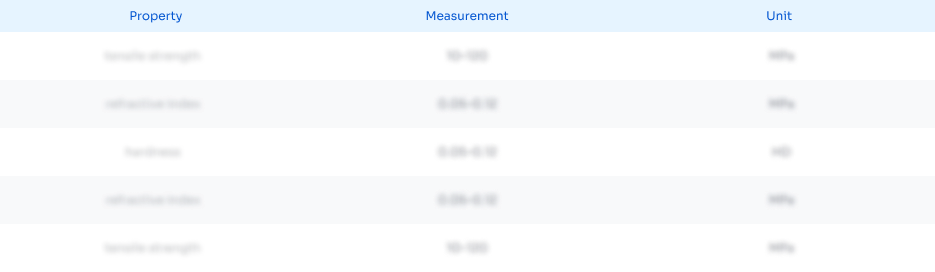
Abstract
Description
Claims
Application Information

- R&D
- Intellectual Property
- Life Sciences
- Materials
- Tech Scout
- Unparalleled Data Quality
- Higher Quality Content
- 60% Fewer Hallucinations
Browse by: Latest US Patents, China's latest patents, Technical Efficacy Thesaurus, Application Domain, Technology Topic, Popular Technical Reports.
© 2025 PatSnap. All rights reserved.Legal|Privacy policy|Modern Slavery Act Transparency Statement|Sitemap|About US| Contact US: help@patsnap.com