Equipment suitable for high-temperature molten material cooling and waste heat recycling
A technology of high-temperature melting and waste heat recovery, applied in lighting and heating equipment, treatment of discharged materials, waste heat treatment, etc. Problems such as low waste heat recovery rate can solve the serious waste of water resources, improve the working environment and reduce energy consumption
- Summary
- Abstract
- Description
- Claims
- Application Information
AI Technical Summary
Problems solved by technology
Method used
Image
Examples
Embodiment Construction
[0049] The present invention will be described in further detail below in conjunction with specific examples, but not as a limitation of the present invention.
[0050] Such as Figure 1-3 As shown, the present invention is suitable for high-temperature molten material cooling and waste heat recovery equipment, and consists of a roller cooler body, a reducer 12, a gear transmission 11, a motor 13, a base 1, an on-site monitoring instrument, and material import and export pipelines, etc. The body of the roller cooling machine includes a shell 3, a pair of rollers 4, a support device 5, an exhaust device 6, a scraper 8 and a feed water cooling device 10.
[0051] The shell 3 is installed on the base 1, and the roller pair 4 is composed of two counter-rotating rollers 401. The rollers 401 are installed in the shell 3 through the support device 5, and the motor 13, deceleration and The device 12 and the gear transmission device 11 are driven to rotate, and the inside of the rolle...
PUM
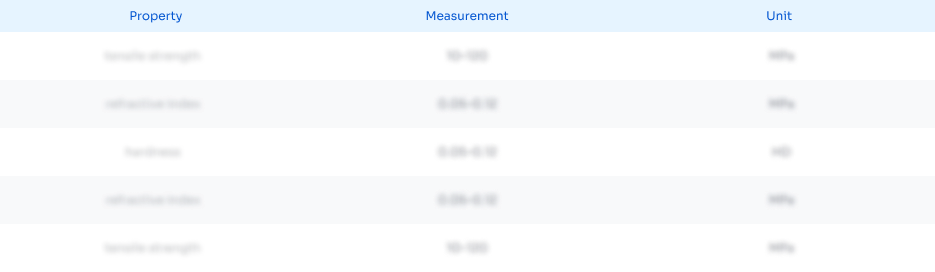
Abstract
Description
Claims
Application Information

- R&D Engineer
- R&D Manager
- IP Professional
- Industry Leading Data Capabilities
- Powerful AI technology
- Patent DNA Extraction
Browse by: Latest US Patents, China's latest patents, Technical Efficacy Thesaurus, Application Domain, Technology Topic, Popular Technical Reports.
© 2024 PatSnap. All rights reserved.Legal|Privacy policy|Modern Slavery Act Transparency Statement|Sitemap|About US| Contact US: help@patsnap.com