Foaming bi-component organic silicon pouring sealant and preparation method thereof
A silicone potting adhesive and two-component technology, applied in the field of silicone potting adhesive and its preparation, can solve the problems of poor foaming uniformity, difficulty in controlling foaming degree and speed, and achieve uniform foaming and flame retardancy. The effect of good performance and simple production process
- Summary
- Abstract
- Description
- Claims
- Application Information
AI Technical Summary
Problems solved by technology
Method used
Image
Examples
Embodiment 1
[0020] Add 50 parts of 2000mPa·s α,ω-dihydroxy polydimethylsiloxane, 45 parts of aluminum hydroxide, 40 parts of aluminum oxide and 10 parts of 30mPa·s polyfunctional hydroxyl silicone resin into 1000L high-speed In a stirred tank, stir in vacuum for 2 hours, the vacuum degree is -0.95MPa, then add 50 parts of 1000mPa·s α,ω-dihydroxy polydimethylsiloxane, 5 parts of hydrogen content of 0.75% Hydrogen-containing silicone oil, 1 part of 2-methyl-3-butyn-2-ol, 3 parts of MQ silicone resin treated with fluoroalcohol, 5 parts of octanol, mixed and stirred at high speed for 0.5h, and then vacuum degassed to obtain component A ; Prereact 100 parts of alkoxy-terminated polydimethylsiloxane with a viscosity of 1000 mPa·s and 10 parts of aminosilane oligomers at a temperature of 100 ° C for 0.5 h, cool to room temperature and mix 25 parts of polysilicic acid Ethyl ester, 20 parts of dimethyldiethoxysilane, 5 parts of KH-792 and 0.05 parts of dioctyltin dilaurate were added to the reacto...
Embodiment 2
[0022] Add 50 parts of 2000mPa·s α,ω-dihydroxypolydimethylsiloxane, 35 parts of aluminum hydroxide, 30 parts of aluminum oxide and 15 parts of 50mPa·s polyfunctional hydroxyl silicone resin into 1000L high-speed In a stirred tank, stir in vacuum for 2 hours, the vacuum degree is -0.95MPa, then add 50 parts of 1000mPa·s α,ω-dihydroxypolydimethylsiloxane, 15 parts of hydrogen content of 0.75% Hydrogen-containing silicone oil, 2 parts of 3-methyl-1-pentyn-3-ol, 10 parts of MQ silicone resin treated with fluoroalcohol, 10 parts of octanol, mixed and stirred at high speed for 0.5h, and then vacuum degassed to obtain component A ; Pre-react 100 parts of alkoxy-terminated polydimethylsiloxane with a viscosity of 1000 mPa·s and 15 parts of aminosilane oligomers at a temperature of 100 ° C for 0.5 h, cool to room temperature and mix 20 parts of orthosilicic acid Add propyl ester, 15 parts of methyltriethoxysilane, 5 parts of KH-792 and 0.3 parts of dioctyltin dilaurate into the reactor...
Embodiment 3
[0024] Add 50 parts of 2000mPa·s α,ω-dihydroxypolydimethylsiloxane, 70 parts of alumina and 20 parts of 30mPa·s polyfunctional hydroxyl silicone resin into a 1000L high-speed stirring tank at room temperature, and stir in vacuum 2h, the vacuum degree is -0.95MPa, then cool to room temperature and add 50 parts of 1000mPa·s α,ω-dihydroxypolydimethylsiloxane, 25 parts of hydrogen-containing silicone oil with a hydrogen content of 0.75%, 5 parts 2-Methyl-3-butyn-2-ol, 15 parts of MQ silicone resin treated with fluoroalcohol, 15 parts of octanol, mixed and stirred at high speed for 0.5h, and then vacuum degassed to obtain component A; 100 parts of viscosity was 1000mPa·s alkoxy-terminated polydimethylsiloxane, 20 parts of aminosilane oligomers were pre-reacted at 100°C for 0.5h, and after cooling to room temperature, 30 parts of polyethyl silicate, 20 parts of dimethicone Methyldiethoxysilane, 5 parts of KH-792 and 0.8 parts of dioctyltin dilaurate were added to the reactor, stirre...
PUM
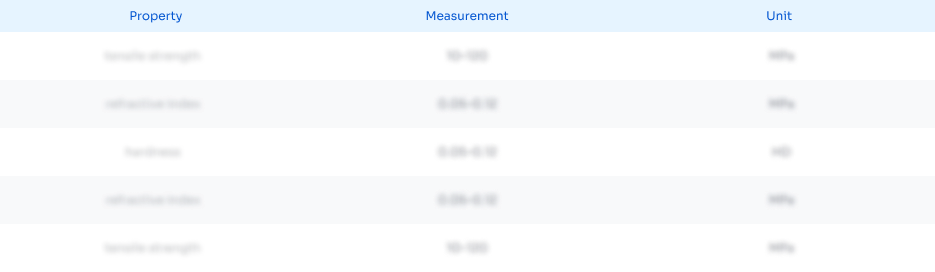
Abstract
Description
Claims
Application Information

- R&D
- Intellectual Property
- Life Sciences
- Materials
- Tech Scout
- Unparalleled Data Quality
- Higher Quality Content
- 60% Fewer Hallucinations
Browse by: Latest US Patents, China's latest patents, Technical Efficacy Thesaurus, Application Domain, Technology Topic, Popular Technical Reports.
© 2025 PatSnap. All rights reserved.Legal|Privacy policy|Modern Slavery Act Transparency Statement|Sitemap|About US| Contact US: help@patsnap.com