Method of utilizing polydopamine modified aluminum nitride microspheres to prepare thermal radiation film
A technology of polydopamine and aluminum nitride, which is applied in the field of heat dissipation materials, can solve the problems of poor heat dissipation performance of heat dissipation film, achieve good thermal conductivity, strengthen heat exchange, and increase the direction of heat flow
- Summary
- Abstract
- Description
- Claims
- Application Information
AI Technical Summary
Problems solved by technology
Method used
Examples
example 1
[0028] Preparation of ground product:
[0029] In parts by weight, put 8 parts of aluminum chloride hexahydrate, 2 parts of cetyltrimethylammonium bromide, 26 parts of distilled water, 6 parts of absolute ethanol and 3 parts of formamide into the beaker, and place the beaker In the resistance heating mantle, put the magnetic ball into the beaker, mix and stir for 2h under the condition of rotation speed of 500r / min and temperature of 60℃ to prepare the mixture;
[0030] Add 10% propylene oxide of the mixed liquid mass to the above beaker, mix and stir for 3 minutes with a stirring device at a speed of 1200r / min. After stirring, let it stand for 20 minutes to prepare a reaction gel. Place the beaker in a vacuum drying oven. Dry for 3 hours under the conditions of a vacuum of 120MPa and a temperature of 70°C, and then put it into a grinder to grind through a 50-mesh sieve to obtain a dried product;
[0031] Put the above-mentioned dry product into a tube furnace, raise the temperature...
example 2
[0038] Preparation of ground product:
[0039] In parts by weight, put 9 parts of aluminum chloride hexahydrate, 3 parts of cetyltrimethylammonium bromide, 27 parts of distilled water, 7 parts of absolute ethanol and 4 parts of formamide into the beaker, and place the beaker In the resistance heating mantle, put the magnetic ball into the beaker, mix and stir for 2.5h under the conditions of speed of 550r / min and temperature of 65°C to prepare the mixture;
[0040] Add 14% propylene oxide of the mixed liquid mass to the above beaker, mix and stir for 4 minutes with a stirring device at a speed of 1250r / min. After stirring, let it stand for 25 minutes to prepare a reaction gel. Place the beaker in a vacuum drying oven. Dry for 3.5 hours under the conditions of a vacuum of 160MPa and a temperature of 75°C, and then put it into a grinder to grind through a 50-mesh sieve to obtain a dried product;
[0041] Put the above-mentioned dry product into a tube furnace, raise the temperature in...
example 3
[0048] Preparation of ground product:
[0049] In parts by weight, put 10 parts of aluminum chloride hexahydrate, 4 parts of cetyltrimethylammonium bromide, 28 parts of distilled water, 8 parts of absolute ethanol and 5 parts of formamide into the beaker, and place the beaker In the resistance heating mantle, put a magnetic ball into the beaker, mix and stir for 3 hours under the conditions of a rotation speed of 600r / min and a temperature of 70°C to prepare a mixture;
[0050] Add 16% propylene oxide of the mixed liquid mass to the above beaker, mix and stir for 5 minutes at a speed of 1300r / min with a stirring device, and let it stand for 30 minutes after stirring to obtain a reaction gel. Place the beaker in a vacuum drying oven. Dry for 4 hours under the conditions of a vacuum of 200 MPa and a temperature of 80 ℃, and then put it into a grinder and grind through a 50-mesh sieve to obtain a dried product;
[0051] Put the above-mentioned dry product into a tube furnace, raise the...
PUM
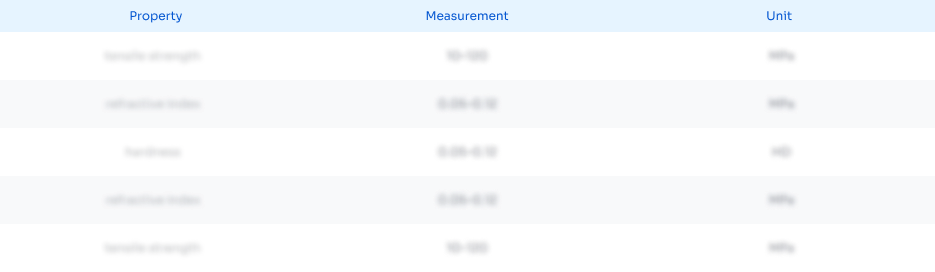
Abstract
Description
Claims
Application Information

- Generate Ideas
- Intellectual Property
- Life Sciences
- Materials
- Tech Scout
- Unparalleled Data Quality
- Higher Quality Content
- 60% Fewer Hallucinations
Browse by: Latest US Patents, China's latest patents, Technical Efficacy Thesaurus, Application Domain, Technology Topic, Popular Technical Reports.
© 2025 PatSnap. All rights reserved.Legal|Privacy policy|Modern Slavery Act Transparency Statement|Sitemap|About US| Contact US: help@patsnap.com