Cold fusion concrete
一种混凝土、五水合物的技术,应用在混凝土材料和制造混凝土材料领域,能够解决没有教导冷融混凝土和水泥等问题
- Summary
- Abstract
- Description
- Claims
- Application Information
AI Technical Summary
Problems solved by technology
Method used
Image
Examples
Embodiment 1
[0062] To produce sand and cement-based materials that can be troweled or poured into place and are resistant to acids, sulfates, chlorides, and heat exposure up to 1,200 degrees Fahrenheit, reagent resistant mineral aggregates such as, but not limited to, high-grade Silica content of alluvial quartzite deposits, quarried basalt or quarried marble with a maximum aggregate size of approximately 1 / 4 inch to #200 US sieve (.0029” or 74 μm), combined in proportion to form a smooth texture veneers, and provide a maximum ply thickness to aggregate size ratio of approximately 3 to 1. This combination will result in no deviation from the line of maximum density when tested on an X / Y diagram and plotted with an increase to 0.45 force % across. Above 35%, the distribution densification level of the aggregate is increased to the maximum. In terms of mass, the combined aggregate should be about 20% (wt / wt) to 75% (wt / wt) of the mass of the final cement-based mixture including water wt). P...
Embodiment 2
[0074] To produce sand, aggregate, and cement-based materials that can be troweled or poured into place, resistant to acids, sulfates, chlorides, and brief (up to approximately 10 minutes) heat exposure of up to 2,400 degrees Fahrenheit, reagent resistant Acceptable materials such as, but not limited to, cenospheres, expanded glass, vermiculite, expanded shale, pozzolan, entrapped air, and other void-creating and lightweight filler materials are combined in proportions that create a cementitious matrix and provide maximum The layer thickness to aggregate size ratio was about 3 to 1. This combination, when examined on an X / Y diagram and plotted at increasing 0.45 force % crossings, will result in deviations from the line of maximum density of up to 35%, increasing the level of densification of the aggregate distribution to a maximum. In terms of mass, the combined aggregate should be from about 5.0% (wt / wt) to about 40% (wt / wt) of the mass of the final cement-based mixture incl...
Embodiment 3
[0086] To produce cementitious mortar materials that can be troweled or poured into place and are resistant to various acids, but especially hydrofluoric acid. Cement-based materials should include at least one of fly ash (Class C or F) and granulated blast furnace slag (GGBFS), alone or in combination, depending on the strength, volume change, carbonation and The rheological behavior is added in variable concentrations up to a mass concentration in the range of a maximum of 65% (wt / wt), typically about 10% (wt / wt) to about 65% (wt / wt). Each of the fly ash concentration and granulated blast furnace slag fines (GGBFS) concentration in the mixture should be selected by balancing the mass and volumetric amounts of each in the mixture design until the properties meet project-specific requirements.
[0087] Cement-based materials should include sodium or potassium metasilicate and / or sodium or potassium metasilicate pentahydrate in variable concentrations depending on the strength,...
PUM
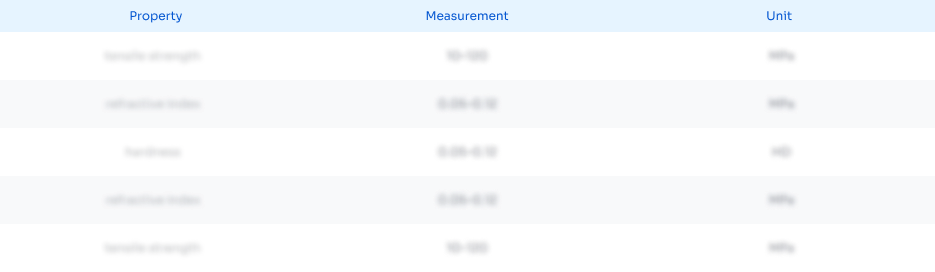
Abstract
Description
Claims
Application Information

- Generate Ideas
- Intellectual Property
- Life Sciences
- Materials
- Tech Scout
- Unparalleled Data Quality
- Higher Quality Content
- 60% Fewer Hallucinations
Browse by: Latest US Patents, China's latest patents, Technical Efficacy Thesaurus, Application Domain, Technology Topic, Popular Technical Reports.
© 2025 PatSnap. All rights reserved.Legal|Privacy policy|Modern Slavery Act Transparency Statement|Sitemap|About US| Contact US: help@patsnap.com