A coating material for light alloy pulping and its preparation method
A coating material, light alloy technology, applied in the direction of coating, etc., to achieve the effect of high defoaming, good film forming and improving service life
- Summary
- Abstract
- Description
- Claims
- Application Information
AI Technical Summary
Problems solved by technology
Method used
Image
Examples
preparation example Construction
[0038] Such as figure 1 As shown, the preparation method of the coating material for light alloy pulping comprises the following steps:
[0039] 1S prepares modified simethicone, anionic and nonionic surfactant compounding agents, co-emulsifiers, water-soluble polymers, regulators and defoamers.
[0040] 2S Add the anionic and nonionic surfactant compounding agent into the water-soluble polymer and stir for 10-20 minutes.
[0041] 3S Add modified simethicone, auxiliary emulsifier, and defoamer to the solution in step 2S and stir together under constant temperature water bath conditions. The stirring time is set at 10-30 minutes, and the water bath temperature is 45-60 degrees Celsius.
[0042] 4S: Add the regulator to the solution obtained in step 3S, and stir at 20-25 degrees Celsius until the solution becomes a uniform and transparent emulsion, stop stirring, and set the stirring time to 60-80 minutes.
[0043] 5S measures the pH value of the emulsion obtained in step 4S, ...
Embodiment 1
[0046] A coating material for light alloy pulping contains the following components, and the content of each component indicates
[0047] as follows:
[0048]
[0049] The coating material used for light alloy pulping in Example 1 has excellent high-temperature wettability, and the coated stirring rod can quickly form a layer of high-temperature resistant, erosion-resistant, micron-scale thick at a temperature as high as 450 degrees Celsius. Uniform film.
Embodiment 2
[0051] A coating material for light alloy pulping contains the following components, and the content of each component is expressed as follows:
[0052]
[0053] The coating material used for light alloy pulping in Example 2 has excellent corrosion resistance and increases the number of uses of the stirring rod. The traditional stirring rod uses hot-work steel H13 material to produce 3000 molds, that is, the surface corrosion is scrapped, and the coating of Embodiment 2 is used. After the material is coated with the stirring rod, the service life is as high as 11000 times.
PUM
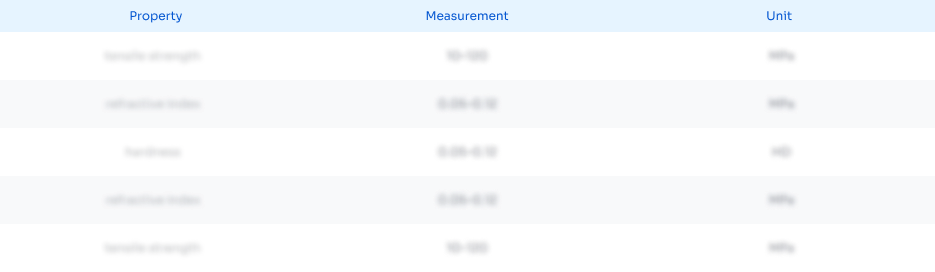
Abstract
Description
Claims
Application Information

- Generate Ideas
- Intellectual Property
- Life Sciences
- Materials
- Tech Scout
- Unparalleled Data Quality
- Higher Quality Content
- 60% Fewer Hallucinations
Browse by: Latest US Patents, China's latest patents, Technical Efficacy Thesaurus, Application Domain, Technology Topic, Popular Technical Reports.
© 2025 PatSnap. All rights reserved.Legal|Privacy policy|Modern Slavery Act Transparency Statement|Sitemap|About US| Contact US: help@patsnap.com