Forging technology of high-strength TC4 titanium alloy column part
A titanium alloy, high-strength technology, applied in the field of titanium alloy forging technology, can solve the problems of the titanium alloy cylindrical forgings producing Widmanstler structure, not meeting product service conditions, improper heating temperature control, etc., to achieve reasonable forging process route, change Morphological characteristics of Widmandelstein microstructure and the effect of reducing temperature gradient
- Summary
- Abstract
- Description
- Claims
- Application Information
AI Technical Summary
Problems solved by technology
Method used
Examples
Embodiment 1
[0071] A high-strength TC 4 The forging process of titanium alloy column parts, the specific steps are as follows:
[0072] Step 1, blanking:
[0073] Carry out size design for the blanking bar, the part size is Φ125×Φ70×240mm, and the raw material is TC 4 Titanium alloy extruded rods, blanked to get the original rods;
[0074] Step 2, car blank:
[0075] Carry out turning processing on the outer circular surface of the original bar obtained in step 1, and process R10 chamfers on the end face of the original bar, and the end face is not allowed to have a center hole, so as to obtain a rough bar;
[0076] Step 3, heating before forging:
[0077] Use an electric furnace to heat the blank bar produced in step 2, put the blank bar in the furnace at room temperature and raise the temperature to 950°C with the furnace;
[0078] Step 4, tool and mold preheating:
[0079] Preheat the upper and lower hammer anvils so that the surface temperature of the anvil surfaces reaches 250°...
Embodiment 2
[0099] A high-strength TC 4 The forging process of titanium alloy column parts, the specific steps are as follows:
[0100] Step 1, blanking:
[0101] Carry out size design for the blanking bar, the part size is Φ125×Φ70×240mm, and the raw material is TC 4 Titanium alloy extruded rods, blanked to get the original rods;
[0102] Step 2, car blank:
[0103] Carry out turning processing on the outer circular surface of the original bar obtained in step 1, and process R10 chamfers on the end face of the original bar, and the end face is not allowed to have a center hole, so as to obtain a blank bar;
[0104] Step 3, heating before forging:
[0105] Heating the blank bar obtained in step 2 with an electric furnace, putting the blank bar into the furnace at room temperature and raising the temperature to 970°C with the furnace;
[0106] Step 4, tool and mold preheating:
[0107] Preheat the upper and lower hammer anvils to make the surface temperature of the anvil surface reac...
Embodiment 3
[0127] A high-strength TC 4 The forging process of titanium alloy column parts, the specific steps are as follows:
[0128] Step 1, cutting:
[0129] Carry out size design for the blanking bar, the part size is Φ125×Φ70×240mm, and the raw material is TC 4 Titanium alloy extruded rods, blanked to get the original rods;
[0130] Step 2, car blank:
[0131] Carry out turning processing on the outer circular surface of the original bar obtained in step 1, and process R10 chamfers on the end face of the original bar, and the end face is not allowed to have a center hole, so as to obtain a blank bar;
[0132] Step 3, heating before forging:
[0133] Use an electric furnace to heat the blank bar produced in step 2, put the blank bar in the furnace at room temperature and raise the temperature to 960°C with the furnace;
[0134] Step 4, tool and mold preheating:
[0135] Preheat the upper and lower hammer anvils so that the surface temperature of the anvil surfaces reaches 260°C...
PUM
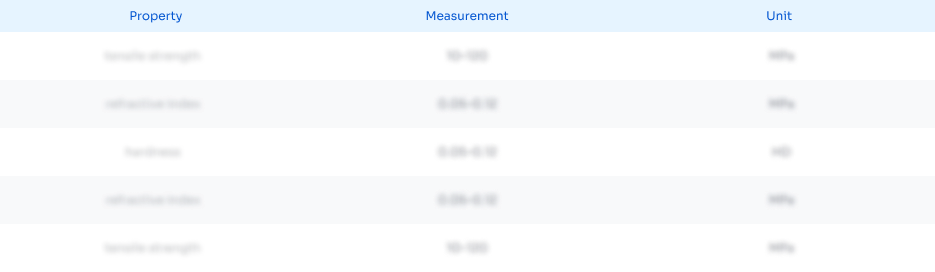
Abstract
Description
Claims
Application Information

- R&D
- Intellectual Property
- Life Sciences
- Materials
- Tech Scout
- Unparalleled Data Quality
- Higher Quality Content
- 60% Fewer Hallucinations
Browse by: Latest US Patents, China's latest patents, Technical Efficacy Thesaurus, Application Domain, Technology Topic, Popular Technical Reports.
© 2025 PatSnap. All rights reserved.Legal|Privacy policy|Modern Slavery Act Transparency Statement|Sitemap|About US| Contact US: help@patsnap.com