Coating type electrolytic rust remover
An electrolytic rust removal and coating technology, applied in the field of rust removal, can solve problems such as affecting painting, normal bonding, declining metal mechanical properties, and increasing processing costs.
- Summary
- Abstract
- Description
- Claims
- Application Information
AI Technical Summary
Problems solved by technology
Method used
Image
Examples
Embodiment 1
[0029] The coating-type electrolytic derusting agent provided in this embodiment includes derusting additives and borosulfate; the derusting additives are: sodium molybdate, copper nitrate, zinc phosphate, zinc dihydrogen phosphate, nickel nitrate, ferrous sulfate;
[0030] The parts by weight of the raw materials of the borosulfate and the derusting additive are respectively: 100 parts of borosulfate, 0.5 part of molybdate, 1 part of copper nitrate, 0.5 part of zinc phosphate, 1 part of zinc dihydrogen phosphate, 0.5 part of nickel nitrate part, 2 parts of ferrous sulfate;
[0031] Wherein the preparation steps of borosulfate are as follows:
[0032] (1) Put 60-100 parts of nonylphenol into the reaction kettle, heat to 120-150°C, then slowly add 3-8 parts of boric acid, and react for 80-100 minutes after the addition;
[0033] (2) After the reaction is completed, the temperature is lowered to 60-100° C., 3-10 parts of auxiliary agent glycerin are added, and the temperature i...
Embodiment 2
[0038] The coating-type electrolytic rust remover provided in this embodiment includes rust remover additives and borosulfate; the rust remover additives are: ammonium molybdate, copper nitrate, zinc phosphate, zinc dihydrogen phosphate, nickel nitrate, ferrous sulfate;
[0039] The parts by weight of the raw materials of the borosulfate and the derusting additive are respectively: 100 parts of borosulfate, 0.8 part of molybdate, 1.5 part of copper nitrate, 0.7 part of zinc phosphate, 1.5 part of zinc dihydrogen phosphate, 0.6 part of nickel nitrate part, 2.5 parts of ferrous sulfate;
[0040] Wherein the preparation steps of borosulfate are as follows:
[0041] (1) Put 60-100 parts of nonylphenol polyoxyethylene ether NP-10 into the reactor, heat to 120-150°C, then slowly add 3-8 parts of boric acid, and react for 80-100 minutes after the addition;
[0042] (2) After the reaction is completed, cool down to 60-100°C, add 3-10 parts of auxiliary agent propylene glycol, and nat...
Embodiment 3
[0047] The coating-type electrolytic rust remover provided in this embodiment includes rust remover additives and borosulfate; the rust remover additives are: sodium molybdate, copper sulfate, zinc phosphate, zinc dihydrogen phosphate, nickel nitrate, ferrous sulfate;
[0048] The parts by weight of the raw materials of the borosulfate and the derusting additive are respectively: 100 parts of borosulfate, 1 part of molybdate, 2 parts of copper nitrate, 0.8 part of zinc phosphate, 2 parts of zinc dihydrogen phosphate, and 1 part of nickel nitrate. part, 3 parts of ferrous sulfate;
[0049] Wherein the preparation steps of borosulfate are as follows:
[0050] (1) Put 60-100 parts of nonylphenol polyoxyethylene ether NP-20 into the reactor, heat to 120-150°C, then slowly add 3-8 parts of boric acid, and react for 80-100 minutes after the addition;
[0051] (2) After the reaction is completed, cool down to 60-100°C, add 3-10 parts of diglycerol as an auxiliary agent, and cool dow...
PUM
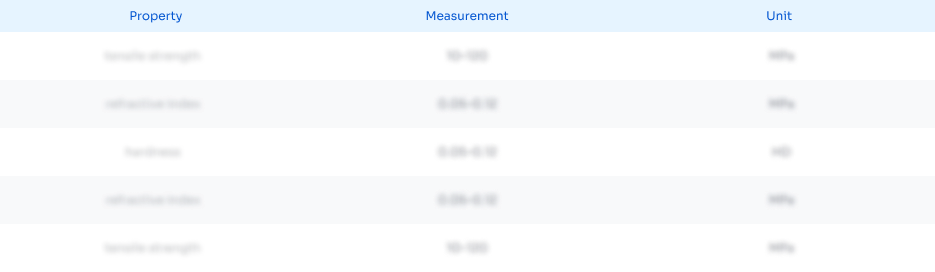
Abstract
Description
Claims
Application Information

- R&D Engineer
- R&D Manager
- IP Professional
- Industry Leading Data Capabilities
- Powerful AI technology
- Patent DNA Extraction
Browse by: Latest US Patents, China's latest patents, Technical Efficacy Thesaurus, Application Domain, Technology Topic, Popular Technical Reports.
© 2024 PatSnap. All rights reserved.Legal|Privacy policy|Modern Slavery Act Transparency Statement|Sitemap|About US| Contact US: help@patsnap.com