Non-leveling surface autonomous identification robot additive manufacturing forming precision control method
A technology of additive manufacturing and precision control, applied in the fields of additive manufacturing and machine vision, it can solve the problems of difficult matching of imaging points of two cameras and complex algorithms, so as to ensure welding quality and stability, high processing precision, and processing process. concise effect
- Summary
- Abstract
- Description
- Claims
- Application Information
AI Technical Summary
Problems solved by technology
Method used
Image
Examples
Embodiment Construction
[0032] Below in conjunction with accompanying drawing and embodiment the present invention will be further described:
[0033] A method for autonomously identifying non-flat surfaces and controlling the forming accuracy of robotic additive manufacturing. The device includes: two M1214-MP2-computar lenses with a focal length of 12mm and an Acer K132 projector (with a resolution of 1280×800) The three-dimensional measurement system, the TIG welding torch and Precitec YC-30 laser laser fixed together by the fixture, the six-axis robot of Japan YASKWA company, the robot control cabinet, the Miller Dynasty350 welding machine, the wire feeder is WF-007A, the welding torch fixture one Set, computer, welding torch water cooling device, shielding gas device.
[0034] Specific implementation steps:
[0035] Step 1: Use an angle grinder to grind the upper surface of the workpiece to be additively manufactured (Q235A substrate, the size is 200mm×200mm×40mm, with uneven surface) to remove...
PUM
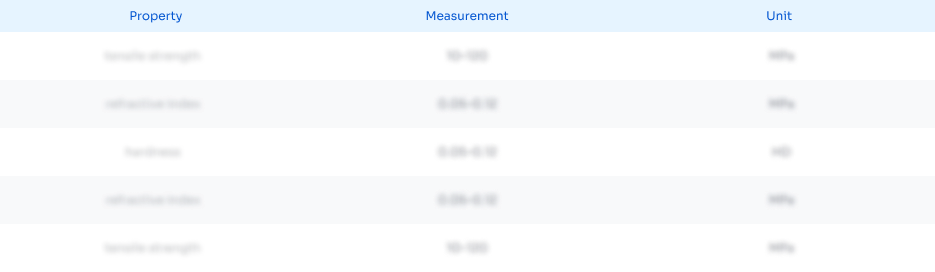
Abstract
Description
Claims
Application Information

- R&D
- Intellectual Property
- Life Sciences
- Materials
- Tech Scout
- Unparalleled Data Quality
- Higher Quality Content
- 60% Fewer Hallucinations
Browse by: Latest US Patents, China's latest patents, Technical Efficacy Thesaurus, Application Domain, Technology Topic, Popular Technical Reports.
© 2025 PatSnap. All rights reserved.Legal|Privacy policy|Modern Slavery Act Transparency Statement|Sitemap|About US| Contact US: help@patsnap.com