Method for improving strength of insulator at discharging end of ignition electric nozzle of aviation engine
An aero-engine and insulator technology, which is used in the field of aviation and aerospace engine ignition, can solve the problems of insulator cracks at the discharge end and reduce the stress on the discharge end of the insulator, and achieve the effects of reduced stress, high efficiency and concentrated ignition.
- Summary
- Abstract
- Description
- Claims
- Application Information
AI Technical Summary
Problems solved by technology
Method used
Image
Examples
Embodiment Construction
[0021] Embodiments of the present invention are described in detail below, and the embodiments are exemplary and intended to explain the present invention, but should not be construed as limiting the present invention.
[0022] In this embodiment, the insulator material and the use environment scene are analyzed, the force of the insulator is theoretically calculated, the improvement plan is determined, and the simulation verification is carried out.
[0023] 1. Insulator material analysis
[0024] The insulator material is GLC-58 alumina ceramics, with Al 2 o 3 as the main body, Al 2 o 3 The content is more than 95%, adding other metal oxide components as additives, mixing evenly according to a certain proportion, and then processing through calcination, ball milling, sieving, plasticizing, molding, aging, bisque firing, roasting, and performance testing. The sintering temperature is 1650-1700°C.
[0025] Ceramic materials are brittle materials, the fracture of brittle m...
PUM
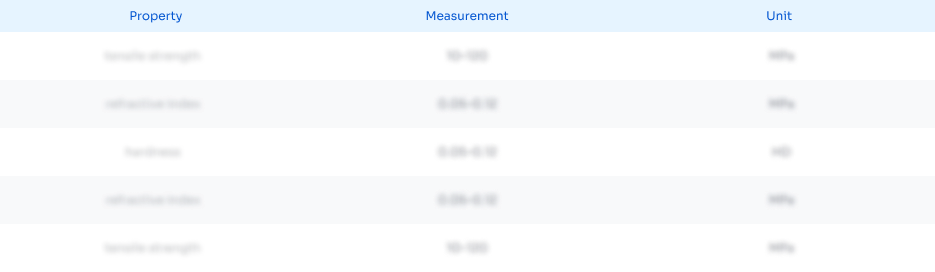
Abstract
Description
Claims
Application Information

- R&D Engineer
- R&D Manager
- IP Professional
- Industry Leading Data Capabilities
- Powerful AI technology
- Patent DNA Extraction
Browse by: Latest US Patents, China's latest patents, Technical Efficacy Thesaurus, Application Domain, Technology Topic, Popular Technical Reports.
© 2024 PatSnap. All rights reserved.Legal|Privacy policy|Modern Slavery Act Transparency Statement|Sitemap|About US| Contact US: help@patsnap.com