Method for recycling steel-ladle hot-state casting residues by means of converter
A technology of casting slag and converter slag, which is applied in the manufacture of converters, etc., can solve the problem that the waste heat of casting slag itself cannot be effectively utilized, and achieve the effects of dephosphorization in the converter, improvement of smelting efficiency, and obvious environmental protection benefits
- Summary
- Abstract
- Description
- Claims
- Application Information
AI Technical Summary
Problems solved by technology
Method used
Image
Examples
Embodiment 1
[0048] The "single slag" process is used to recycle hot casting slag from the ladle.
[0049] Step 1: Use a 120-ton converter to conduct the test. After the steel is tapped, the slag operation is adopted, and an average of 350kg of magnesium balls are added. The slag splashing time is 3.8 minutes on average. The final slag splashing is all left in the converter. The molten iron is mixed into the converter for "single slag" process operation.
[0050] Step 2: The average amount of casting slag added is 3.4 tons, and the average amount of steel tapping is 125 tons. When the blowing slag material starts to melt, start to add lime in small quantities, and the average amount of lime added is 33.41kg / t steel (one pour After that, add lime on average 950kg), light burnt dolomite 13.40kg / t steel, sintered ore 5.5kg / t steel, magnesium balls average 10.07kg / t steel. The average oxygen supply time is 14.09min (the average oxygen supply time is 0.86min after pouring), and the oxygen cons...
Embodiment 2
[0055] The "double slag" process is adopted for the recycling of hot casting slag.
[0056] Step 1: Use a 120-ton converter to conduct the test. After the steel is tapped, use the slag operation. Add an average of 320kg of magnesium balls. The average slag splashing time is 3.5 minutes. The molten iron is mixed into the converter for "double slag" process operation.
[0057] Step 2: The average amount of casting slag added is 3.3 tons, and the average amount of steel tapping is 125.1 tons. When the blowing slag material under the blowing gun starts to melt, lime is added in small quantities in multiple batches, and the average amount of lime added is 28.99kg / t steel (one pour After that, add lime on average 850kg), light burnt dolomite 13.69kg / t steel, sintered ore 9.35kg / t steel, magnesium balls average 7.12kg / t steel. The average oxygen supply time is 14.56min (the average oxygen supply time is 1.05min after pouring), and the oxygen consumption is 46.1Nm 3 / t, gas recovery...
Embodiment 3
[0062] The "single slag" process is used to recycle hot casting slag from the ladle.
[0063] Step 1: Use a 120-ton converter to conduct the test. After the steel is tapped, use the slag operation, add 250kg (2kg / t steel) magnesium balls, splash the slag for 3 minutes, and leave the final slag splashed in the converter. The molten iron of casting slag is blended into the converter for "single slag" process operation.
[0064] Step 2: Add 4 tons of casting slag and 125 tons of steel tapping. When the blowing slag starts to melt, start to add lime in small batches. The amount of lime added is 44kg / t steel (625kg of lime is added after one pour , that is, 5kg / t steel), light-burned dolomite 12kg / t steel, sintered ore 8.1kg / t steel, and magnesium balls an average of 9.05kg / t steel. The average oxygen supply time is 14.9min (the oxygen supply time is 0.5min after one pour), and the oxygen consumption is 45.4Nm 3 / t, gas recovery 96.6Nm 3 / t. The smelting cycle is 37.5min.
[0...
PUM
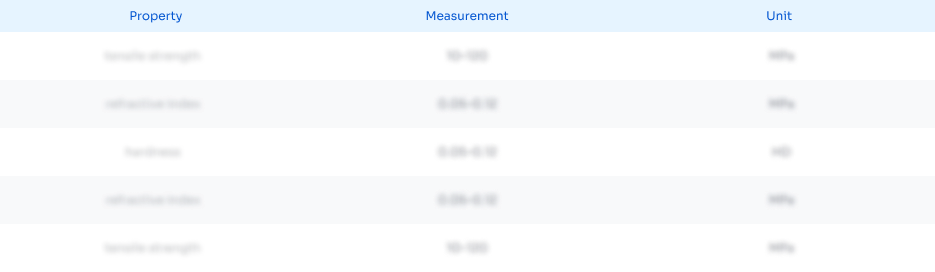
Abstract
Description
Claims
Application Information

- R&D
- Intellectual Property
- Life Sciences
- Materials
- Tech Scout
- Unparalleled Data Quality
- Higher Quality Content
- 60% Fewer Hallucinations
Browse by: Latest US Patents, China's latest patents, Technical Efficacy Thesaurus, Application Domain, Technology Topic, Popular Technical Reports.
© 2025 PatSnap. All rights reserved.Legal|Privacy policy|Modern Slavery Act Transparency Statement|Sitemap|About US| Contact US: help@patsnap.com