Method and device for forming stepped cylindrical member through laser impact
A technology of laser shock and cylindrical parts, which is applied in the forming of high-precision complex shape parts, and the field of laser shock forming stepped cylindrical parts, which can solve the problems of failure to improve the forming depth of metal sheets, exceeding the forming speed of metal sheets, and limiting metal sheets Formability and other issues can be achieved to reduce thermal effects, save processing time, and improve impact effects
- Summary
- Abstract
- Description
- Claims
- Application Information
AI Technical Summary
Problems solved by technology
Method used
Image
Examples
Embodiment Construction
[0024] The forming process of forming a three-step stepped cylindrical part according to the present invention will be described in detail below with reference to the accompanying drawings.
[0025] The device of the present invention includes a laser loading system, a mold forming system, a mixed liquid system and a control system; The pulsed laser beam 4 is generated by the laser 3, and the pulsed laser beam 4 is reflected by the total reflection mirror 5 during propagation, and after passing through the convex lens 15, it is irradiated on the suspended carbon particles 9 and the absorbing layer 20; the mold forming system Including die 23, metal sheet 21, absorption layer 20, constraining layer 19, blank holder 22, screw 18, large stud 24, small stud 25, large nut 26, small nut 27 and mechanical arm 17; die 23 Connect with the big stud 24 through threads, a small stud 25 is nested in the big stud 24, and the big stud 24 and the small stud 25 are connected through threads, a...
PUM
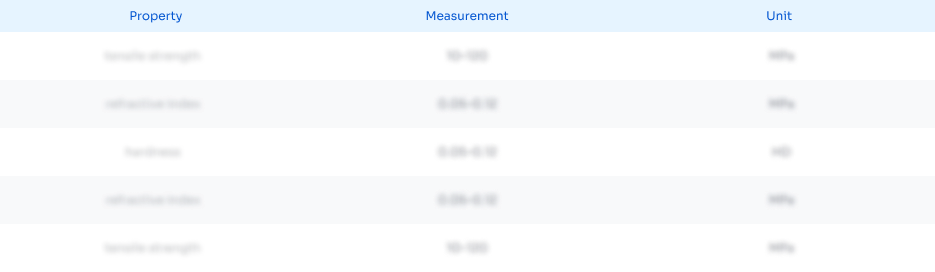
Abstract
Description
Claims
Application Information

- R&D
- Intellectual Property
- Life Sciences
- Materials
- Tech Scout
- Unparalleled Data Quality
- Higher Quality Content
- 60% Fewer Hallucinations
Browse by: Latest US Patents, China's latest patents, Technical Efficacy Thesaurus, Application Domain, Technology Topic, Popular Technical Reports.
© 2025 PatSnap. All rights reserved.Legal|Privacy policy|Modern Slavery Act Transparency Statement|Sitemap|About US| Contact US: help@patsnap.com