Automatable steel plate spring production process
A production process, the technology of automobile steel plate, applied in the field of automobile parts processing, can solve the problems of high cost, no obvious improvement in the service life of physical properties and mechanical properties, and the small application range of materials, etc., to achieve extended service life and high elastic limit , use the effect of safety
- Summary
- Abstract
- Description
- Claims
- Application Information
AI Technical Summary
Problems solved by technology
Method used
Image
Examples
Embodiment 1
[0048] Automobile leaf springs are manufactured according to the following process: blanking, straightening, machining, ear rolling, heat treatment, shot blasting, primer, final assembly, preloading, and topcoat. Among them, the steel plate material is 60Si 2 Mn, 50CrVA, SUP9 (55CrMnA), 55SiMnVB, heat treatment according to the following steps:
[0049] a. Place the leaf spring in a heating furnace and heat it. Among them, 60Si 2 Mn steel is heated to 990±20°C, 50CrVA steel is heated to 980±20°C, SUP9 (55CrMnA) steel is heated to 960±20°C, 35SiMnVB steel is heated to 850±20°C, and kept for 50 minutes;
[0050] b. Immerse the leaf spring in an aqueous solution containing 8% sodium chloride and 0.1% polyvinyl alcohol at 60°C, and pass helium into the aqueous solution, quench and cool for 80s;
[0051] c. Rinse the quenched leaf spring, place it in a tempering furnace, heat it to 500-540°C, keep it warm for 50 minutes, and then cool it down to room temperature.
Embodiment 2
[0053] Automobile leaf springs are manufactured according to the following process: blanking, straightening, machining, ear rolling, heat treatment, shot blasting, primer, final assembly, preloading, and topcoat. Among them, the steel plate material is 60Si 2 Mn, heat treatment according to the following steps:
[0054] a. Place the leaf spring in a heating furnace, heat it to 990±20°C, and keep it warm for 25 minutes;
[0055] b. Immerse the leaf spring in an aqueous solution containing 3% sodium chloride and 0.3% polyvinyl alcohol at 40°C, and pass helium into the aqueous solution, quench and cool for 50s;
[0056] c. Rinse the quenched leaf spring, place it in a tempering furnace, heat it to 600°C, keep it warm for 45 minutes, and then cool it down to room temperature.
Embodiment 3
[0058] Automobile leaf springs are manufactured according to the following process: blanking, straightening, machining, ear rolling, heat treatment, shot blasting, primer, final assembly, preloading, and topcoat. Among them, the steel plate material is 60Si 2 Mn, heat treatment according to the following steps:
[0059] a. Place the leaf spring in a heating furnace, heat it to 990±20°C, and keep it warm for 40 minutes;
[0060] b. Immerse the leaf spring in an aqueous solution containing 3% sodium chloride and 0.3% polyvinyl alcohol at 75°C, and pass helium into the aqueous solution, quench and cool for 200s;
[0061] c. Rinse the quenched leaf spring, place it in a tempering furnace, heat it to 500°C, keep it warm for 90 minutes, and then cool it down to room temperature.
PUM
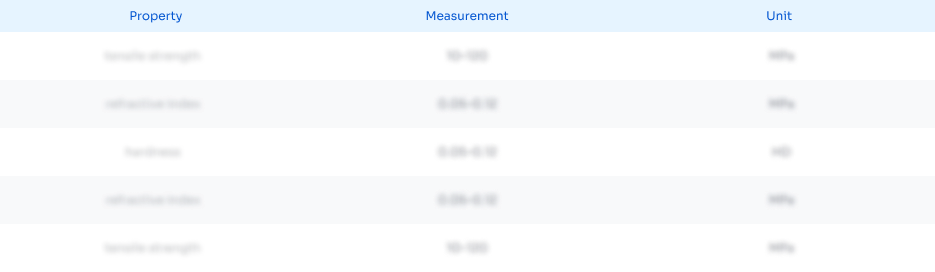
Abstract
Description
Claims
Application Information

- R&D
- Intellectual Property
- Life Sciences
- Materials
- Tech Scout
- Unparalleled Data Quality
- Higher Quality Content
- 60% Fewer Hallucinations
Browse by: Latest US Patents, China's latest patents, Technical Efficacy Thesaurus, Application Domain, Technology Topic, Popular Technical Reports.
© 2025 PatSnap. All rights reserved.Legal|Privacy policy|Modern Slavery Act Transparency Statement|Sitemap|About US| Contact US: help@patsnap.com