Short-flow pre-treatment method for pure cotton heavy fabrics
A heavy-duty fabric, short-process technology, applied in fiber processing, plant fibers, textiles and papermaking, etc., can solve the problems of high strength loss of pure cotton heavy fabrics, reduced cellulose molecular weight, and difficulty in enlarging the reaction device, and achieve mechanical properties. Excellent, good mechanical properties, the effect of improving the feel
- Summary
- Abstract
- Description
- Claims
- Application Information
AI Technical Summary
Problems solved by technology
Method used
Image
Examples
Embodiment 1
[0034] Pure cotton thick plain weave gray cloth (C12×12 52×50 1 / 1 63"197g / m 2 ) scouring and bleaching liquid padding, its scouring and bleaching liquid consists of: scouring agent 2g / L, caustic soda 10g / L, hydrogen peroxide (35%) 4g / L, sodium silicate 4g / L, fatty alcohol polyoxyethylene ether 2g / L , The excess rolling rate is 80%, the steaming temperature is 95°C, and the steaming time is 20min. After steaming, wash with hot water first, then cold water. The pure cotton heavy fabrics washed with steam and water are mercerized with 130g / L sodium hydroxide as a low-alkali solution, and finally fully washed and dried.
Embodiment 2
[0036] Singeing pure cotton thick twill yarn card gray fabric (C10×10 74×44 3 / 1↖43" / 57" 283g / m 2 ) scouring and bleaching liquid padding, its scouring and bleaching liquid consists of: scouring agent 10g / L, caustic soda 8g / L, hydrogen peroxide (28%) 12g / L, sodium silicate 5g / L, fatty alcohol polyoxyethylene ether 4g / L , The excess rolling rate is 100%, and the cold stacking time is 0.5h. The piled pure cotton heavy fabrics were steamed at a steaming temperature of 98° C. and a steaming time of 30 minutes. After steaming, wash with hot water first, then cold water. The pure cotton heavy fabrics after steam washing are lightly bleached with dilute hydrogen peroxide solution. The time is 3 minutes. After light bleaching, wash in cold water. The pure cotton heavy fabric after light bleaching is mercerized with a concentration of 140g / L sodium hydroxide as a low-alkali solution, and finally fully washed with water and dried.
Embodiment 3
[0038] Singeing pure cotton thick twill thread card gray fabric (C40 / 2×40 / 2 141×76 2 / 2↗43" / 57" 260g / m 2 ) scouring and bleaching liquid padding, its scouring and bleaching liquid consists of: scouring agent 15g / L, caustic soda 2g / L, hydrogen peroxide (30%) 15g / L, oxygen bleaching stabilizer sodium silicate 5g / L, fatty alcohol polyoxyethylene Ether 6g / L, excess rate 100%, cold pile time 1h. The piled pure cotton heavy fabrics were steamed at a steaming temperature of 100° C. and a steaming time of 60 minutes. After steaming, wash with hot water first, then cold water. The pure cotton heavy fabric after steam washing is mercerized with a concentration of 140g / L sodium hydroxide as a low-alkali solution, and finally fully washed and dried.
PUM
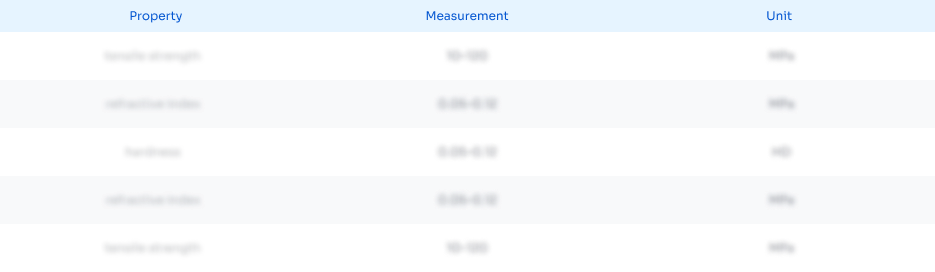
Abstract
Description
Claims
Application Information

- R&D
- Intellectual Property
- Life Sciences
- Materials
- Tech Scout
- Unparalleled Data Quality
- Higher Quality Content
- 60% Fewer Hallucinations
Browse by: Latest US Patents, China's latest patents, Technical Efficacy Thesaurus, Application Domain, Technology Topic, Popular Technical Reports.
© 2025 PatSnap. All rights reserved.Legal|Privacy policy|Modern Slavery Act Transparency Statement|Sitemap|About US| Contact US: help@patsnap.com