Functional self-flame-retardant coating material
A flame retardant coating and functional technology, applied in the field of water-based functional coatings, can solve the problems of environmental and human hazards, easy powdering of flame retardants, and many organic solvents, and achieve low price, good adhesion, and leveling. Good results
- Summary
- Abstract
- Description
- Claims
- Application Information
AI Technical Summary
Problems solved by technology
Method used
Examples
Embodiment 1
[0022] A kind of water-based alkyd self-flame retardant resin A, its preparation process is as follows:
[0023] a) In a four-port reactor equipped with a thermometer, condenser, water separator, and agitator, add 6.5 parts of linseed oil, 6.5 parts of phthalic anhydride, 3.5 parts of propylene glycol, 6.3 parts of pentaerythritol, and dihydroxy 2.0 parts of methacrylic acid, 2.6 parts of isophthalic acid, start heating, after the material in the kettle melts completely, pass into N 2 , start stirring and raise the temperature to 165°C-180°C, add 2.0 parts of benzoic acid, 1.8 parts of stearyl alcohol and 10.0 parts of reflux solvent xylene, keep the temperature for 2-3 hours, remove the water brought out by the reflux reaction, and cool down The reflux solvent is circulated in the reactor;
[0024] b) When little or no water is separated, raise the temperature to 190°C for 1-1.5 hours, then raise the temperature to 200°C for 1-1.5 hours, then raise the temperature to 210-220...
Embodiment 2
[0028] A kind of water-based alkyd self-flame retardant resin B, its preparation process is as follows:
[0029] a) In a four-port reactor equipped with a thermometer, a condenser, a water separator, and an agitator, 7.0 parts of tung oil, 5.5 parts of acetic anhydride, 3.0 parts of neopentyl glycol, and trimethylol were sequentially added in parts by weight according to the formula 6.5 parts of propane, 2.0 parts of dimethylolpropionic acid, 3.0 parts of adipic acid, start heating, when the material in the kettle is completely melted, feed N 2 , start stirring and raise the temperature to 165°C~180°C, add 1.5 parts of benzoic acid, 1.2 parts of stearyl alcohol and 10.0 parts of reflux solvent xylene, keep the temperature for 2~3 hours, remove the water brought out by the reflux reaction, and cool down The reflux solvent is circulated in the reactor;
[0030] b) When little or no water is separated, raise the temperature to 190°C for 1-1.5 hours, then raise the temperature to...
Embodiment 3
[0034] Put 16.2 parts of deionized water, 0.3 parts of wetting agent, 0.8 parts of dispersant, and 0.2 parts of defoamer into the mixing tank according to the weight ratio of the formula, and stir evenly; add 4.5 parts of mica powder and 8.0 parts of titanium dioxide under high-speed dispersion , 6.0 parts of barium sulfate, 0.2 parts of pH regulator, then slowly add 60.0 parts of water-based alkyd self-flame retardant resin A with low-speed stirring, stir for 20-25 min, then add 3.0 parts of alcohol ester twelve, 0.2 parts of thickener, 0.1 part of foaming agent, 0.3 part of leveling agent, 0.2 part of fungicide, stir for 10-15 minutes, filter and pack.
PUM
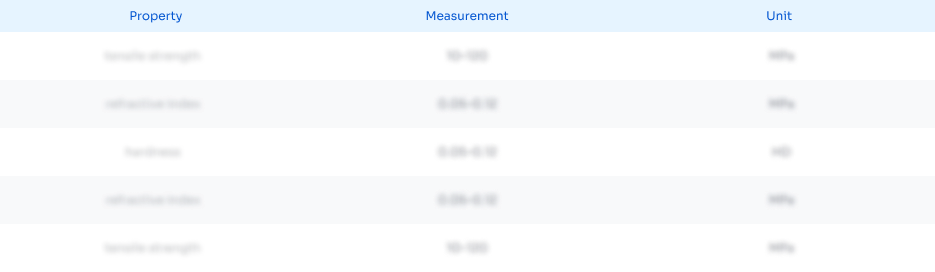
Abstract
Description
Claims
Application Information

- Generate Ideas
- Intellectual Property
- Life Sciences
- Materials
- Tech Scout
- Unparalleled Data Quality
- Higher Quality Content
- 60% Fewer Hallucinations
Browse by: Latest US Patents, China's latest patents, Technical Efficacy Thesaurus, Application Domain, Technology Topic, Popular Technical Reports.
© 2025 PatSnap. All rights reserved.Legal|Privacy policy|Modern Slavery Act Transparency Statement|Sitemap|About US| Contact US: help@patsnap.com