A preparation method of light-weight wallboard and multi-layer light-weight wallboard
A light-weight wallboard and fabric technology, applied in the field of building materials, can solve the problems of low strength and inconspicuous sound insulation effect, achieve low thermal conductivity, improve overall mechanical properties, and improve sound insulation effect
- Summary
- Abstract
- Description
- Claims
- Application Information
AI Technical Summary
Problems solved by technology
Method used
Image
Examples
preparation example Construction
[0018] A kind of preparation method of lightweight wallboard provided by the embodiment of the present invention, it comprises the following steps:
[0019] S1, pre-processing
[0020] Please refer to figure 1 , the pre-processing process is the operation before the cloth, this process needs to be operated according to the state of the raw material, if you choose the right raw material, you can omit the pre-processing process. Generally speaking, the pretreatment process includes: pulverizing the first ingredient and the second ingredient to 6-10 mesh, performing granulation treatment and aging for 20-28 hours.
[0021] Specifically, in the operation process, the components in the first ingredient and the second ingredient are uniformly mixed and then pulverized; it is also possible to pulverize separately and then mix. The pulverization process can adopt the method of ball milling, and after pulverization, sieve to obtain materials meeting the particle size requirements. S...
Embodiment 1
[0043] This embodiment provides a formula for lightweight wallboard, including the first ingredient and the second ingredient. In parts by weight, the first ingredient includes 12 parts of tailings slag, 3 parts of waste brick powder, 12 parts of pressed mud, and polishing slag. 50 parts, 3 parts of glass powder, 0.3 parts of silicon carbide and 0.7 parts of sodium tripolyphosphate; the second ingredient includes 12 parts of tailings slag, 3 parts of waste brick powder, 8 parts of pressed mud, 60 parts of polishing slag, 2 parts of bentonite, carbonized 0.2 parts of silicon, 0.3 parts of ferric oxide and 0.7 parts of sodium polyphosphate.
[0044] The present embodiment also provides a method for preparing a multi-layer lightweight wallboard, which uses the above formula, and the specific steps include:
[0045] Firstly, crush the first ingredient and the second ingredient to about 6 mesh and carry out iron removal treatment, then carry out spray granulation and stale for 20 h...
Embodiment 2
[0049] This embodiment provides a formula for lightweight wallboard, including the first ingredient and the second ingredient. In parts by weight, the first ingredient includes 16 parts of tailings slag, 7 parts of waste brick powder, 18 parts of pressed mud, and polishing slag. 60 parts, 8 parts of glass powder, 0.4 parts of silicon carbide and 0.8 parts of water glass; the second ingredient includes 16 parts of tailings slag, 7 parts of waste brick powder, 13 parts of pressed mud, 70 parts of polishing slag, 6 parts of bentonite, and 0.3 parts of silicon carbide 0.4 part, 0.4 part of ferric oxide and 0.8 part of water glass.
[0050] The present embodiment also provides a method for preparing a multi-layer lightweight wallboard, which uses the above formula, and the specific steps include:
[0051] Firstly, the first ingredient and the second ingredient are crushed to about 10 mesh and iron removal treatment is carried out, and then they are respectively sprayed and granulat...
PUM
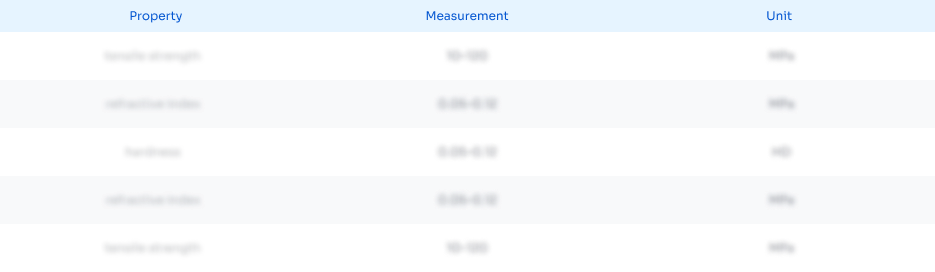
Abstract
Description
Claims
Application Information

- R&D
- Intellectual Property
- Life Sciences
- Materials
- Tech Scout
- Unparalleled Data Quality
- Higher Quality Content
- 60% Fewer Hallucinations
Browse by: Latest US Patents, China's latest patents, Technical Efficacy Thesaurus, Application Domain, Technology Topic, Popular Technical Reports.
© 2025 PatSnap. All rights reserved.Legal|Privacy policy|Modern Slavery Act Transparency Statement|Sitemap|About US| Contact US: help@patsnap.com