Metallurgical chemical solid waste recycling system and method thereof
A solid waste, metallurgical chemical technology, applied in the field of metallurgical chemical solid waste resource utilization system, can solve the problem that the quality of nickel-chromium-iron alloy products cannot be guaranteed to meet relevant standards and customer requirements, the product does not meet the requirements of nickel-chromium-iron alloy products, and copper elements cannot be guaranteed. It has not been rationally utilized and other problems, and has achieved the effects of thorough harmless treatment, high degree of equipment mechanization and automation, and good economic and social benefits.
- Summary
- Abstract
- Description
- Claims
- Application Information
AI Technical Summary
Problems solved by technology
Method used
Image
Examples
Embodiment 1
[0048] Embodiment 1 (pre-reduction equipment uses rotary kiln)
[0049] Resource utilization of stainless steel waste (nickel, chromium)
[0050] The chemical composition of stainless steel waste is shown in Table 1 below
[0051] Table 1 Chemical composition of stainless steel waste
[0052]
[0053] According to the chemical composition content of the waste in Table 1, in this embodiment, the specific formula and the calculation of the quantity of relevant metal elements (metal tons) are shown in the following table 2 with the amount of production and treatment waste as 10,000 tons on a dry basis:
[0054] Table 2 Calculation table of waste formula and metal element quantity
[0055]
[0056] The technical process and specific operation steps of this embodiment are shown in figure 2 shown.
[0057] in, figure 2 The auxiliary raw materials in the PLC batching shown in step 6 include slagging agent, secondary slag of returned iron (washed iron), etc., and the redu...
Embodiment 2
[0075] Resource utilization of electroplating sludge
[0076] The present embodiment electroplating sludge chemical composition and formula calculation are shown in the following table 4
[0077] Table 4 Calculation table of chemical composition and formula of electroplating sludge
[0078]
[0079] For the process steps of electroplating sludge resource utilization image 3 shown.
[0080] image 3 The intermediate pre-reduction equipment adopts a sintering machine, and in the process operation steps, except that the ball making operation in step 4 is not required, the rest of the operations are the same as in Example 1.
[0081] For nickel-copper alloy products, if other element components need to be refined according to the customer's requirements, the relevant refining operation of step 8 can be continued.
[0082] The present embodiment nickel-copper alloy chemical composition analysis and metal element recovery calculation are shown in table 5 below
[0083] Tabl...
Embodiment 3
[0093] Resource utilization of nickel-containing waste
[0094] The nickel-containing waste described in this embodiment mainly refers to the nickel-containing waste catalyst in the production process of petrochemical industry and other industries, and its chemical composition and formula calculation are shown in Table 6 below
[0095] Table 6 Chemical composition and formula calculation table of spent nickel-containing catalyst
[0096]
[0097] The pre-reduction equipment of this embodiment is produced using a shaft kiln;
[0098] The process steps of this embodiment are shown in Figure 4 shown.
[0099] The operation of step 1 to step 8 in the illustration in this embodiment is the same as that of embodiment 1, and the refining in step 9 is to carry out dephosphorization and decarburization refining in the modulation electric furnace and AOD respectively, to prepare low-carbon, low-phosphorus high-quality nickel-iron alloy products .
[0100] The present embodiment ...
PUM
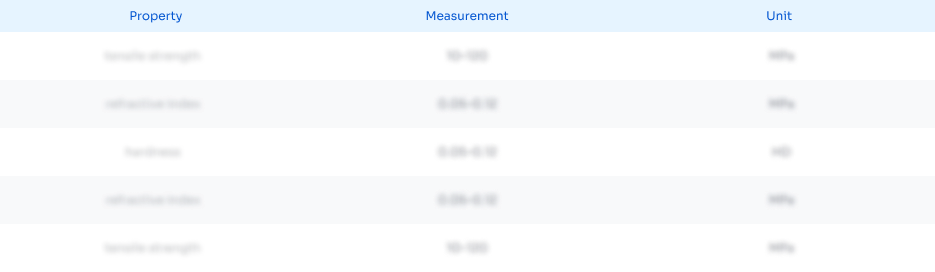
Abstract
Description
Claims
Application Information

- R&D Engineer
- R&D Manager
- IP Professional
- Industry Leading Data Capabilities
- Powerful AI technology
- Patent DNA Extraction
Browse by: Latest US Patents, China's latest patents, Technical Efficacy Thesaurus, Application Domain, Technology Topic, Popular Technical Reports.
© 2024 PatSnap. All rights reserved.Legal|Privacy policy|Modern Slavery Act Transparency Statement|Sitemap|About US| Contact US: help@patsnap.com